The price of ensuring quality in chemical manufacturing goes far beyond cost. Hopefully, quality problems are caught before they can affect patients but even then, such problems can make or break a manufacturing organization. In the U.S., while it takes significant effort to earn and maintain cGMP standards, quality control can be the difference between a CMO’s success and failure in the race to commercialize vital drugs.
One of the key areas that best-in-class companies need to consider to ensure the most effective standards of quality in the lab is in cleaning of equipment and ensuring clean room operations.
Cleaning of Equipment
Facilities that manufacture multiple products may share the same equipment, which can significantly increase the potential for cross-contamination. So it’s critical that extreme caution be taken to properly clean equipment. cGMP requires that cleaning procedures and the analytical methods used for analysis of their samples are demonstrated to be effective and repeatable, which is known as validation of cleaning procedures and analytical methods. By assessing the toxicity and potency of existing residue on potential human consumers of the next product to be manufactured in the same equipment, labs can reduce the levels of existing process residue to meet a predetermined specification.
Rinsing, soaking, or spraying equipment surfaces with a liquid-medium, boiling a solvent inside the enclosed space of a piece of equipment, or manual scrubbing or wiping of equipment surfaces are all different cleaning techniques. The appropriate cleaning techniques are determined based on equipment design, yet choice of cleaning techniques may also be limited by the nature of the residue. If a residue (e.g. certain polymers) is not soluble in any known solvent, the choice of cleaning technique is limited to those that rely heavily on mechanical force such as manual scrubbing/wiping or impingement by a high-pressure liquid stream.
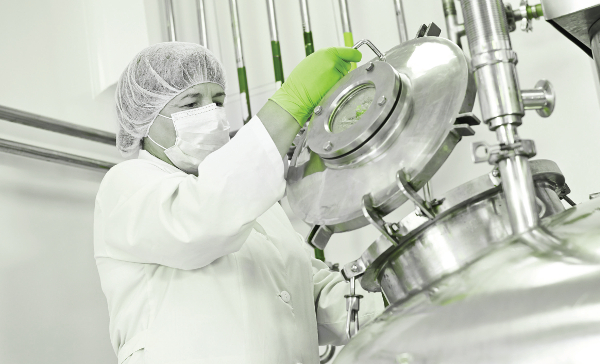
The effectiveness of a cleaning procedure is demonstrated by analyzing rinse and swab samples taken from equipment. In order to obtain a sample that is representative of the entire surface area of a piece of equipment, a rinse sample is taken from a set volume of solvent that has been routed throughout the equipment system and has come in to contact with almost all wet surfaces of the equipment system. Swab samples are taken by wiping predetermined locations of the equipment system (swab locations) with specialized swabs. Swab locations are usually those that are poorly or not covered by a rinse, such as geometrically restricted sites, and are deemed to be on the most difficult to clean pieces of equipment.
Ensuring Clean Room Operations
When working with Active Pharmaceutical Ingredients (APIs), special precautions must be taken to prevent contamination of final products. Strong quality assurance and quality control systems ensure raw materials and consumables meet internal and external standards. A key area that can be overlooked as a potential microbial or particulate contamination source is the packaging and production environment. To control this contamination, especially in final packaging and sensitive processes, cleanroom environments are often used.
The FDA defines a cleanroom as “a room designed, maintained, and controlled to prevent particle and microbiological contamination of drug products. Such a room is assigned and reproducibly meets an appropriate air cleanliness classification.” Cleanrooms for API manufacturing are used for drug products with high sensitivity to airborne particulates and microbes. Cleanroom quality is maintained through room architecture, air filtration, and control of personnel.
One step companies take to ensure clean room operations is to have each room include its own air filtering unit which is maintained at a positive pressure in relation to the outside environment to protect the integrity of the atmosphere. Additionally, personnel working inside separate units can be connected via a hallway which is used as a gowning area. Only personnel trained on internal SOPs regarding GMP manufacturing should be permitted in this area. Other controls such as full-body suits, dust masks, respirators, and hairnets ensure human contact is not a source of biological contamination. Clean room operations should also not be confined to the lab. Production areas and packaging rooms should be FDA and ICH Q7-compliant to ensure that final products are packaged in a controlled environment.
By implementing processes to ensure that equipment is continuously clean and that clean room operations are in place, today’s chemical manufacturing operations not only ensures regulatory compliance, but also earn their spot as an organization that puts quality above all else.
Ed Price is President of PCI Synthesis (www.pcisynthesis. com), a 15-year-old custom chemical manufacturer of new chemical entities (NCEs), generic active pharmaceutical ingredients (APIs), and other specialty chemical products.