Outsourcing of non-core activities continues to be a value-driven calculus, as the biopharmaceutical manufacturing industry remains very much focused on productivity gains. However, there are signs that the outsourcing landscape has moved beyond its traditional concentration on non-core activities. The outsourcing decision has become a more strategic one that takes into account key CMO capabilities that are sometimes not available in-house.
In BioPlan Associates’ 10th Annual Report and Survey of Biopharmaceutical Manufacturing Capacity and Production [1], more than 200 developers and CMOs from around the world were surveyed to obtain an in-depth view of outsourcing today. Results suggest that the market is not only growing, but changing.
How Much Biomanufacturing Activity is being Outsourced?
Data from this study indicates that outsourcing strategies for production by biotherapeutic developers has evolved over the past number of years, with the more pronounced transitions coming for newer systems:
- Mammalian cell culture: Percentage of facilities outsourcing “No Production” (i.e., performing all production in-house) has declined from 57.6% in 2006 to 46.2% in 2013;
- Microbial systems: There has been a recent shift downward in inhouse production, (58.1% performing all production in-house in 2006, up to 64.2% in 2010, before decreasing to 34.8% in 2013);
- Yeast systems: An overall trend toward more outsourcing – 50% in 2013 did not outsource any production, the lowest proportion to date, down from 60-85% over the prior 7 years;
- Insect cell system: A similarly small 37.5% outsourced no production, down from 65-100% in years past.
It is noted that there is considerably less data to work with when it comes to plant and insect systems, such that the results for those systems tend to be subject to greater variance from one year to the next.
The data clearly shows that more facilities are outsourcing at least some of their production. And further results from the study serve as a preview of more outsourcing to come:
- Mammalian cell culture: 36.6% of facilities expect to keep all operations in-house in 2018, compared to the 42.6% who currently report no outsourcing;
- Microbial fermentation: 24% expect to still not be outsourcing any production in 2018, compared to 34.8% currently keeping all production in-house; and
- Yeast systems: Only 41.7% expect to be manufacturing 100% in-house in five years’ time, vs 50% in 2013 doing so.
Interestingly, fewer respondents expect to be outsourcing some plant and insect cell operations in 2018 than currently report doing so, implying that some of those who are currently outsourcing production expect to cease doing so at some point in the next few years.
Still, more than half of insect cells and plant users surveyed believed that they will be outsourcing by 2018. For plant cells and insect cells, relatively few organizations have wanted to hand over these areas to outside control, but these attitudes might be shifting. This trend has continued to grow, in general, over at least the past five years. For example, 25% of respondents in 2007 projected that over the next five years they would be outsourcing projects involving insect cells. That more than doubled to 55.6% in 2013. With respect to plant cells, 33.3% of companies in 2007 indicated that this would be an area for outsourcing over the next five years, and that grew to 57.1% in 2013
Activities Most Commonly Outsourced
Analyzing the types of activities typically being contracted out offers more insight into the extent of outsourcing occurring today. To evaluate this, respondents were presented with a list of 24 different areas in which outsourcing is taking place, asking them to identify which activities from the list they are currently outsourcing.
Figure 1. Biopharmaceutical Manufacturing Facilities Outsourcing NO Production, 2006-2013It was found that a majority of respondents are outsourcing, to some degree, all but 5 of the activities, with the remaining 5 activities being outsourced to some extent by at least 4 in 10 respondents.
According to this study, the most commonly outsourced activity today is analytical testing (other bioassays), with about 9 in 10 respondents reporting outsourcing at least some of this relatively specialized activity. The reason for this is likely related to the need for highly specialized staff to run these assays and prepare related regulatory filings, as well as to have the expensive, high-maintenance equipment in rather constant operation. This percentage outsourced will likely increase in the future, with regulatory agencies looking for more characterization and other data about products.
Plant maintenance services (81.5%) and toxicity testing (75.3%) were next on the list, with validation services (71.6%) and fill/finish operations (70.4%) rounding out the top 5.
At the other end of the spectrum, a minority of respondents reported currently outsourcing any upstream production operations (48.1%), downstream (44.4%) and upstream (43.2%) process development, design of experiments (DoE; 43.2%) and QbD services (42%).
Even for these less commonly-outsourced activities, the trends are clearly pointing toward more outsourcing. For example, 2013’s 48.1% claiming some outsourcing of upstream production operations was a marked rise from 20.7% just 3 years earlier. Similarly, the 44.4% outsourcing downstream process development in 2013 was roughly double the count (22.1%) from 2010, and the jump has been even larger for upstream process development (from 17.1% in 2010 to 43.2% in 2013).
The following statistic probably summarizes the increased enthusiasm toward outsourcing best of all: Of the 24 areas tracked since 2010, 2013’s results showed the most widespread level of outsourcing to-date in all but one (product characterization testing, which has become outsourced by fewer respondents relative to years past).
However, it is important to keep in mind that these figures refer to the percentage of companies who are outsourcing these activities to some degree. When the approximate percentage of each activity that is currently being outsourced is taken into account, the numbers change.
Respondents reported outsourcing close to one-third of their analytical testing (other bioassays – 32.2%) and fill/finish operations (31.8%), and more than one-quarter (28.6%) of their toxicity testing. Going further down the list, the extent of outsour cing became smaller.
Outsourcing activity is still growing by this measure, but the increases are not across the board. The largest increase is for analytical testing of other bioassays, from an average of 18.9% outsourced in 2010 to 2013’s average of 32.3%. The extent to which API biologics manufacturing is being outsourced is also on the rise, more than doubling between 2010 (7.9%) and 2013 (19.4%).
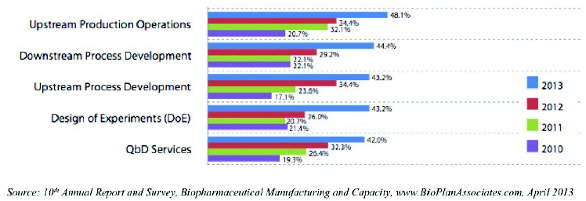
Figure 2. Percent of Biomanufacturers Outsourcing At Least Some Activity Today, Select Areas
Other increases are more incremental in nature, while some activities were outsourced to a lesser extent in 2013. Among those, fill/ finish operations – down from an average 36.5% outsourced in 2010 to 31.8% in 2013 – and cell line development, down slightly from 12.8% to 10.9%. The smoother trends by this metric likely reflect the entrance of new facilities into the outsourcing landscape, with these new clients likely beginning their outsourcing of these activities at more tepid levels than those who have been outsourcing them for longer periods.
The prospects for outsourcing in some areas are better than others:
- Validation services: Specialized validation service providers have been around for quite some time, and their prospects remain solid. Few biopharmaceutical manufacturers are large enough to have sufficient critical mass to maintain manufacturing systems validation expertise in-house. The increasing use of single-use systems, including increased future use for commercial product manufacture, will likely result in further use of and spending on validation services, given some unique validation challenges posed by single-use systems. For example, it can cost up to $100,000 or more to develop the testing and documentation needed for each major plastic, e.g., the exposed layer of bioreactor bag liners, in contact with the product being manufactured.
- Media optimization: This is a complex area for companies when it comes to understanding the methods used, ‘know-how’ and related intellectual property. While some companies still rely on standard commercially available media, most large companies as well as CMOs have developed their own ‘trade secrets’ around their upstream processes and are typically very careful and sensitive in sharing this information. This is among the reasons why outsourced “media development” is not a widespread field for outsourcing by most companies, as most already using their own in-house formulations and additives. Also, it is increasingly desirable to combine media selection and optimization with bioprocess design, rather than the traditional practice of seeking to optimize media after the process has been developed.
- APIs: APIs (active agents) outsourcing to CMOs is a long-running business, at least two decades old. With many marketed recombinant proteins coming off-patent in the near future, biosimilar developers worldwide will likely seek the services of CMOs. Given that a substantial share of biosimilar developers cannot lay claim to their own biomanufacturing facilities – and that a significant number of follow-on versions are successful for each current successful product – we can expect that the CMO market will profit from biosimilars development, with API biologics manufacturing in particular an area of demand.
Where in the World is Outsourcing Going?
The predicted strong growth of biosimilars will likely provide major market cGMP manufacturing expertise to CMOs worldwide, and will lead to increased competitiveness – and competition – among commercial-scale-capable biopharmaceutical CMOs. While estimating the exact number of biopharmaceutical CMOs that exist world-wide today is difficult, the majority currently offer early-stage R&D manufacturing services, while fewer support clinical scale manufacture and only a few have the expertise and capabilities to provide full US/EU cGMP-level commercial product manufacturing services. The maturation of CMOs will change that – and data from this report, along with BioPlan Associates’ Wiki www.Top1000Bio.com website [2] – shows ranking and location of biopharma facilities globally. This site gives us some perspective on which regions in the world are poised to profit most from increased demand for outsourcing services.
As part of the study, 25 countries were identified as potential outsourcing destinations, asking respondents to consider their 5-year time horizon and evaluate their facility’s current plans for future international capacity expansion. Where respondents did not see a current need for outsourcing, it seems their answers reflect hypothetical choices nonetheless.
Among all respondents, the US ranked highest as a potential outsourcing destination, with 26.3% (up from 16.9% in 2012) of respondents indicating that there was a “likelihood” or “strong likelihood” that they would outsource production to facilities there.
Given that the survey sample featured a large portion of respondents from the US, this signals a high level of perception of the US as the top off-shoring country by those outside the US. Following the US as potential outsourcing destinations were Singapore and Germany, each cited by 15.8% of respondents, moving in opposite directions from 13.9% and 16.9%, respectively, in 2012. India and the UK, both at 14%, closed out the top five.
In a fairly marked turnaround, 2012’s top potential destination, China, was relegated to the ninth spot in 2013, behind countries such as Ireland, Austria, and Australia. In fact, just 10.6% of respondents said they consider it a potential outsourcing destination, a large retreat from 2012’s 26.2%. This is not unexpected, as China continues to evolve its regulations permitting contract manufacturing of pharmaceuticals.
It was very interesting to see India and China took steps back in 2013’s survey, reversing trends from prior years. This could be a function of an increased focus on regulatory issues noted elsewhere in the study, a focus that carries a lack of confidence that these countries will be able to come up to full US and EU cGMP standards by 2018. Additionally, concerns about IP may have increased in 2013, with India beginning to implement compulsory licensing (abrogating granted patents) for multiple products.
In addition, it should be noted that China was a late entrant in the area of contract manufacturing, and its laws limiting operations of CMOs are challenging. Respondents may have based their views off indications that these may not change in the near future. The few internationallybased CMOs (and partnerships) in China are striving to establish a global presence, though, including working to attain US and EU cGMP standards. Although legal and regulatory aspects hinder commercial-scale contract manufacturing in China, the excess (bio)pharmaceutical production capacity there may permit improvements when the idle capacity of many production facilities can be dealt with.
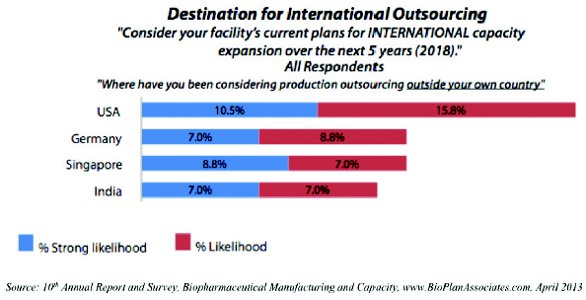
Figure 3. Selected Country Selections as Destination for International Outsourcing of Biomanufacturing
China and India certainly have the capacity to meet demand. The top1000bio.com website estimates that together these two countries account for about one-sixth of global biopharmaceutical manufacturing capacity, split almost evenly between them (China: 8.6%; India 8.1%). Those numbers by themselves virtually assure that these countries will be widely discussed as potential destinations for years to come.
Some countries have over- and under-sized influence relative to their capacity. For example, 7.1% of respondents indicated a likelihood of outsourcing to Russia in the next five years (remember that only 10.6% said the same about China) - although Russia and other Eastern European countries combined account for just 2.9% of biomanufacturing capacity. By comparison, only 8.8% cited Japan and 3.6% Korea as likely destinations, even as Japan and other Asian countries (excluding China and India) comprise almost 10% of global capacity.
Outsourcing Industry Becoming More Technical and International
While 2013’s data points to a renewed focus on traditional biomanufacturing hubs at the expense of newer, emerging markets, there’s plenty of reason to believe that this will not be the case for the long-term. It may be that newer markets are tasked with less value-added services until clients become more comfortable with them, at which point they will be asked to fulfill more technical assignments currently performed in traditional biomanufacturing clusters.
There are numerous incentives that point to more technical outsourcing. These include the need for access to enabling technology, lack of internal expertise (amongst available staff or specialized expertise), response to competitive pressures, and a desire to avoid technology licensing fees and royalties, such as for expression systems. With outsourcing budgets starting to expand again (up by an estimated 1.7% in 2013 among respondents following declines in years past), demand for more highly technical outsourcing will likely take root and also expand internationally.
References
- 10th Annual Report and Survey of Biopharmaceutical Manufacturing Capacity and Production, April 2013, Rockville, MD www. bioplanassociates.com/10th
- See BioPlan’s Top 1000 Global Biopharmaceutical Facilities Index™, http:// www.top1000bio.com. Accessed October 23, 2013
Survey Methodology
The 2013 Tenth Annual Report and Survey of Biopharmaceutical Manufacturing Capacity and Production yields a composite view and trend analysis from 238 responsible individuals at biopharmaceutical manufacturers and contract manufacturing organizations (CMOs) in 30 countries. The methodology also included over 158 direct suppliers of materials, services and equipment to this industry. The 2013 study covers such issues as: new product needs, facility budget changes, current capacity, future capacity constraints, expansions, use of disposables, trends and budgets in disposables, trends in downstream purification, quality management and control, hiring issues, and employment. The quantitative trend analysis provides details and comparisons of production by biotherapeutic developers and CMOs. It also evaluates trends over time, and assesses differences in the world's major markets in the U.S. and Europe.
Eric S. Langer is president and managing partner at BioPlan Associates, Inc., a biotechnology and life sciences marketing research and publishing firm established in Rockville, MD in 1989. He is editor of numerous studies, including “Biopharmaceutical Technology in China,” “Advances in Large-scale Biopharmaceutical Manufacturing”, and many other industry reports. [email protected] 301-921-5979. www. bioplanassociates.com