What are some of the current critical issues facing the industry in regards to packaging requirements and regulations?
Mr. Christoph Blümer, Director Quality, Clinical Supply Services, Catalent Pharma Solutions, Schorndorf, Germany: Within the clinical trial supply arena, one of the most significant changes on the horizon is the impending rollout of the European Commission’s Clinical Trial Regulation (CTR) EU No. 536/2014 Annex VI. Currently, studies within EMEA member states are governed under Directive 2001/20/EC, which requires ‘Period of Use’ information to be placed on a product’s outer packaging only. Under Annex VI however, Period of Use dates will be required to be shown on both the immediate, primary packaging AND the secondary packaging. To further complicate matters, there is a one year transition period after 536/2014 Annex VI goes into effect, where newly submitted studies may opt to use the “old” system under the 2001 directive, and studies submitted prior to the effective date will have three years to adopt the new standards. In addition, new supply models that make late-stage customization of clinical supplies possible, such as Demand-Led Supply, are attracting the attention of clinical sponsors seeking ways to make clinical supply chains more flexible and efficient. These new approaches create challenges in setting up global clinical supply chains capable of fast turnaround times. Plus, massive pressure now being placed on shortening timelines is effectively removing safety buffers intended to accommodate unexpected events, resulting in execution expectations that are not always realistic.
Mr. Mathias Bayru, Group Product Manager, Drug Delivery Solutions, Catalent Pharma Solutions, Schorndorf, Germany: Serialization continues to feature in many companies’ plans in an effort to prevent product counterfeiting and substitution. Serialization is now mandatory in many countries, but because serialization regulations vary from country to country, pharmaceutical companies face previously unprecedented complexity, cost, and risk in implementing strategies that anticipate future regulatory change in different parts of the world. We are advising partners that are trying to grapple with these shifting goals that they should develop a Serialization Master Plan for a global implementation that ‘bakes in’ flexibility.
As the industry is looking for more and more personalized medicines and patient-centric treatments that provide the right dosing - especially with special patient populations - a packaging device could help provide a better way to dose and administer a treatment, perhaps that is appropriate to a child’s weight rather than their age, where there is much heterogeneity. The challenge of course is in providing the right combination of dose and device, as one solution may not work for all.
Oral doses that are low in weight are a big challenge for the industry too, especially when a dose lower than 100 mg is required. The technical challenges and equipment limitations oblige the industry to use experienced partners that have the right capabilities and experience to execute these dosing and packaging operations reliably.
David Kudla, General Manager for North America, Unither Pharma-ceuticals and Rao Tatapudy, R.Ph., Ph.D., Executive Director, Research & Development, Unither Pharmaceuticals: Serialization/track and trace is a major issue, especially due to upcoming compliance deadlines in many regions around the world. Temperature control and managing the cold chain is of particular importance for biologic drugs, especially those shipped to developing countries with limited infrastructure.
Other crucial drivers in packaging technology development are the growing expectations for patient-centric treatment solutions and products that lead to greater medication adherence. Packaging technology is also seen today as providing a mechanism for differentiating drug products and extending their lifecycles as they come off patent.
Jeffrey Reid, Strategic Markets Manager, DWK Life Sciences Inc.: Compound pharmacies are going through the most regulatory changes in the pharmaceutical industry. This mainly stems from the New England Compounding Center (NECC) meningitis outbreak in 2012, which resulted in over 50 deaths. Compounders are now forced to follow the same cGMP that traditional pharmaceutical companies follow to eliminate any sterility issues.
It is important that compound pharmacies work with packaging vendors who have complete manufacturing traceability and have Quality Management Systems (QMS) in place so they reduce the chances of drug issues coming from the packaging system.
Jonathan Gardiner, Packaging Technologist, Almac Group: Currently the biggest challenge facing the pharmaceutical industry, in regards to packaging requirements and regulations, is the pending requirement for serialization. There have been many articles written about serialization, but, in simple terms, it involves the printing of a unique identifier, typically a 2D barcode, on each saleable unit pack, in an effort to combat the growing problem of counterfeit medicines. As well as the additional software and hardware required to print the serialized information, there are also considerations as to the impact on the pack presentation. Careful consideration must be given to any limitations/processing restrictions of the serialization equipment, such as how the product is presented to the printer; what area is required for the serialization information to be printed and verified; and how multiple units are going to be collated, in order for aggregation to be performed. In some respects, the greater challenge is to ensure existing marketed products are serialization friendly, as opposed to the “blank canvas” of a new product.
Can you tell us about some packaging technologies and/or materials that are helping pharmaceutical companies bring new products to market or are reviving older products?
Bayru: As previously mentioned, combination products that include the product itself and a dosing device can improve patients’ experience and increase adherence to a treatment. The right combination may help improve dosing and reduce side effects. Smart devices can even assist patients who have difficulty following their treatment regimens, and can provide helpful reminders that a dose is due, prevent accidental overdose, or inform medical staff when medications are not taken at the right times.
There is a long history of innovation in packaging development and perhaps none is more familiar to us all than in the way that a pack is opened - or not opened as the case may be! It is a challenge to develop a package that protects the drug, can be opened by the intended user, especially if we consider limitations of some user-groups such as the elderly or infirm, but that also offers protection from being opened by children, who are often particularly adept at finding ways of opening containers that may have not have even been considered by development teams. New opening features such as laser-cuts on stick packs or the ability to peel individual tablet blisters foils can help improve the patient experience if implemented well.
New types of primary packaging dosing, such as stick packs or unit dose solutions, can help revive older products by introducing new features for patients or for consumers of OTC products. These may include ‘on-the-go’ versions of existing OTC products and more hygienic forms of dispensing medicines.
Transparent foils, in combination with colored granules or pellets can be used to improve the patient’s experience and boost perceptions of a brand over other products.
Blümer: Digital display labels (eLabels) for clinical trial packaging seem to have made a certain “comeback” without having ever been established in the market outside of small pilots here and there. While the potential of the technology is fascinating as an alternative to traditional, bulky booklet labels and for ease of updating expiry dates on clinical trial materials, questions mostly centered around risk and quality remain. From a regulatory standpoint, the technology appears to be viable, but practically speaking it is still quite cost-intensive at this point although industry groups, most notably TransCelerate BioPharma Inc., have initiatives underway to promote the understanding and adoption of smart technologies. Still, the technology holds promise as it has been successfully adopted in other industries so the real-world proof of concept is there. A technology that was considered old-fashioned is returning and Radio Frequency Identification (RFID) is again being discussed as an alternative to barcode-based patient kit handling for the distribution of clinical materials. This is because RFID offers certain advantages to the automated tracking of materials and, as with other areas of our everyday lives, many new solutions are centered around leveraging the evolving reality of the digital world and that help improve connectivity and efficiency.
Kudla and Tatapudy: Packaging technologies that enable the preparation of single-unit dose products are playing a key role in addressing the issues outlined previously. Single-use dosage forms are often highly portable, as well as convenient and easy to use - even when patients are on the go. This allows medicine to be taken correctly regardless of where a patient is. In addition, single-unit dosage forms offer consistent, reliable and appropriate dosing for some of the most challenged patient populations, particularly children and geriatric patients. For instance, Unither’s sterile blow-fill-seal (BFS) and liquid or powder stick pack dosage forms were developed as a result of our singular focus on providing convenient, modern dosage forms to meet patient needs
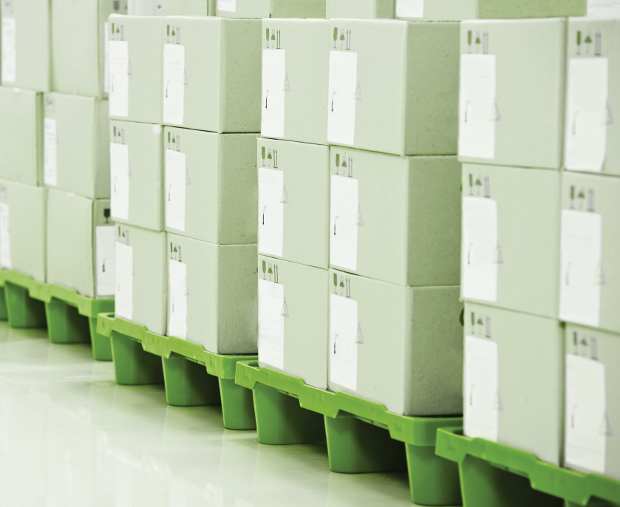
Reid: There has been an increase in nuclear medicine research. Nuclear medicines are made from radioactive substances and are meant to treat several forms of cancer. I have found that these drug products are extremely expensive and are usually a low volume injectable; therefore, it is critical to get the entirety of the product out of the container. At DWK Life Sciences we have a solution known as the WHEATON® V-Vial which has a conical shape on the bottom of the vial unlike a traditional serum vial which has a flat bottom. This allows for the end-user to reduce product waste by up to 99%.
Gardiner: Almac recognizes that in order to be a market leader and maintain a competitive advantage, we need to utilize the most current techniques and strategies and continue to invest in new technologies and equipment. We have seen a significant increase in the number of our clients gaining approval for orphan/niche products. Additionally the requirement to develop pediatric doses, has led to a reduction in batch sizes. This requirement is driving a need to develop more flexible packaging solutions. One processing output has seen Almac invest in various offline and online print technology, specifically Hapa Blisterjet. This is a single color, fully digital, ultra violet piezo inkjet printing system, used for printing both blank and pre-printed blisters. This printer is capable of printing on multiple surfaces which includes aluminium foil, paper-backed foil, PVC and Tyvek. By packaging the tablets or capsules into unprinted blisters and off-line printing these blank blisters, through the Hapa unit, it allows processing of smaller country specific batches at a more efficient scale. It also facilitates just-in-time production and eliminates the requirement to hold large amounts of inventory of both printed material and finished goods. This solution is, and will be, of significant value to those companies launching orphan and niche blistered drug products into EU and ROW markets, many of which Almac already supports.
When a pharmaceutical company is choosing a packaging provider, what questions should they ask? What qualities and expertise should packaging providers have to ensure that their client gets the best quality product?
Blümer: The first question a sponsor company, or their packaging provider, should always ask is what will be the direct or indirect impact of their decisions or actions on the patient? Looking for a packaging provider who is keenly patient-focused is very important.
Bayru: And sponsors should look for proven expertise in the packaging services required, as well as sufficient overall capacity, and the capabilities to be able to offer alternative supply networks and better solutions too.
A firmly instilled “right first time” quality culture is very important and, of course, the provider has to be able to demonstrate a robust Quality Management System (QMS) is in place and that the necessary expertise for the project is available, including an appropriate project management system that is flexible, accountable, and offers appropriate lines of communication at many levels in the sponsor company and the solutions provider.
Kudla and Tatapudy: Packaging can impact the stability and efficacy of the drug product it contains. Pharmaceutical companies must ensure that their packaging providers recognize that packaging is crucial to product performance and not simply the method by which they are dispensed. Compatibility with the product, appropriateness for the patient population, encouragement of compliance, deterrence of counterfeiting, and communication of necessary information are each important aspects of pharmaceutical packaging that must be taken into account.
Contract packagers ideally should have expertise in technologies that provide a competitive advantage to their pharmaceutical customers. A demonstrated history of developing innovative solutions is also desirable. In fact, the ability of packagers to provide cost-savings through the use of innovative designs and novel material choices is essential. Firms also need to be able to collaborate with customers and other service providers to incorporate packaging design early on in the development cycle and reduce both development times and costs.
Reid: It is critical to work with a packaging vendor that has in-house quality and technical support teams who can assist with pre and post sales inquiries. Also, it is important that vendors can offer a complete packaging system so there are no compatibility issues. An example would be a vendor who supplies not only vials but stoppers and seals too.
Lastly, working with packaging vendors who can provide value added services such as particulate cleaning, depyrogenation, sterilization, surface treatments and bar coding; this saves pharmaceutical companies time and labor performing those services in-house.
DWK Life Sciences offers these unique services, taking the complexity that goes with packaging drug products and thus providing our customers with a ready-to-use product, accelerating their time to market. This allows for pharmaceutical companies to focus on their core competency, which is developing and manufacturing pharmaceutical drug products.
Gardiner: Relevant questions to any packaging provider should include
- What Standard Operating Procedures do you have in place to ensure control and consistency of all packaging processes? Look for packaging component supplier management; artwork control & incoming packaging QC testing, as some examples.
- What experience do you have supporting product launches? Ask for client references.
- Show me a standard process flow/project plan for a packaging project.
As a Packaging Technologist it is my responsibility to assess which packaging provider is most appropriate for specific components. There are many factors to be considered, including scale and flexibility of processes and equipment. As a CDMO, with significant experience in supporting the launches of niche and orphan products, we, in turn, need our packing suppliers to be flexible and responsive, with the ability to expedite orders to support rapid product launches. We are often dealing with modest order volumes, over multiple SKUs, so we require that flexibility without compromising on cost-effectiveness and quality of product.
How has the globalization of the pharmaceutical industry affected pharmaceutical packaging? How do you ensure that packaged products meet individual country regulations?
Blümer: Globalization within the pharmaceutical industry has helped to not only support growth of multinational clinical studies, but has also helped local governments see the potential benefit of attracting global study sponsors to their respective countries. In recent years, governments including China, Brazil, and Japan have introduced modifications to their clinical trial laws designed to encourage greater participation from global companies. Close cooperation between the sponsor, CRO and packaging company are key to meeting individual country regulations and keeping projects on track from beginning to end. Packaging providers must have strong regulatory knowledge on both a global and regional level, especially when it comes to helping small customers navigate the regulatory environment.
As studies become increasing global, so does the clinical supply chain. Designed to operate on a global level but to be executed locally, today’s supply chains are increasingly built on a global backbone augmented by one or more regional networks. New supply models are being introduced to improve the flexibility and efficiency of these supply chains. For example, the smaller and more frequent packaging batches characteristic of a demand-led supply model have allowed batch sizes to shrink to just 5% of what they were only five years ago.
What future packaging innovations do you foresee? How will they help pharma companies deliver their products?
Blümer: New supply models such as those that allow late-stage customization, and a demand led approach, will help pharma companies maintain more flexible, efficient, and responsive supply chains. This can improve supply chain performance and lead to potential savings in time and waste as well. The use of high-performance barcode scanning systems and similar technologies; designed to improve material flow and safeguard quality; will become extensive.
In addition to new supply chain models and other technological advances, will be the continued exploration and adoption of new technologies such as the “Digital 4.0” apps that promise to support medication plans for clinical trials or link to data capturing devices such as wearable activity trackers included as part of the patient kit.
Kudla and Tatapudy: Drug manufacturers today need to provide new treatments that exhibit measurable, improved outcomes compared to the existing standards of care - and at the lowest possible cost. Pharmaceutical packaging plays a major role in achieving that goal. No longer does packaging serve to only protect the product; it provides a mechanism for tracking products and maintaining their safety and efficacy. If designed correctly, packaging can make taking medicines an easy experience for patients. As a result, effective pharmaceutical packaging is now seen as a value-added component that can provide real competitive advantage. We expect to see continued interest in novel single-unit dose forms that address concerns for patients and caregivers at home, in the clinic, in the hospital and in nursing homes. Demand for customized packaging solutions that address the specific needs of smaller patient populations will also steadily increase. New anti-counterfeiting solutions will be introduced as well.