Can you assure customers their product is kept at the proper specifications from the manufacturer site to the end-user location? Is there proof?
Introduction
This article completes a series of five articles written to inform the reader about the importance of product temperature control. The first article dealt with the clinical study, the worldwide clinical network of internal and external distribution systems and the risk exposure in distribution. The second article created a model to identify shipping excursions, assess cost and productivity losses. The third article explained the effect of fuel price fluctuations and weight/volume size of packaging on total distribution cost; the importance of shipping excursions as a multiplying factor for cost and additional resources; a list of proven approaches/solutions to move forward was provided. The fourth article explained new technologies now in use in pre-qualified shippers, a breakthrough in thermal materials along with new temperature and humidity devices.
Shipping Lane Dynamics
What we do know about the shipping lane is that it changes frequently. The elements needed for distribution: the product, the shipping container, mode of transport, routes of transportation, manual handling, the temperature monitor and administrative activities are all factors that consistently change.
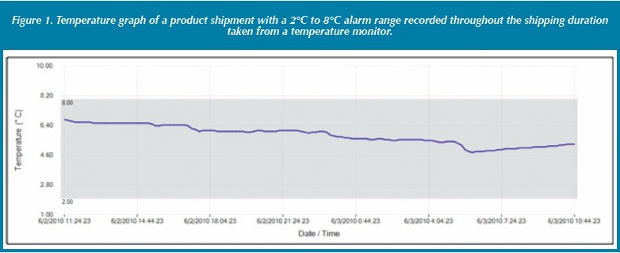
It goes without saying; companies constantly work to cover their risk, since failure on the shipping lane may mean loss of product, increased freight and labor costs, falling short of customer's expectations and/or loss of procedural controls. To address this need, end-users have sought prequalified shipping containers in hopes of simplifying procedures, eliminating temperature monitors and associated costs [5]. However, in some cases, current shipping systems that do not use temperature monitoring suffer from the lack of detection of the product condition and/or documentation of the shipping lane.
The Importance of Temperature Monitoring
Under regulatory methods the absence of temperature monitoring is no doubt a risky activity for a temperature-sensitive product shipment. With temperature monitoring at least there is a verifiable means to detect whether a temperature problem exists with the product during shipment [4]. Temperature monitoring:
- identifies temperature exposure of the product in-transit
- documents and provides data to confirm control and/or detect a problem(s)
There are other questions about the shipment such as: Where was the product located at a specific date/ time? What mode (air, ground, etc.) was used at a specific date/time? These questions arise when a shipping deviation requires an explanation or action about results that are out of specification.
Figure 1 shows the temperature for the product as it moves through the shipping lane. These graphs were prepared and used mainly when a shipping excursion occurred and investigation was conducted. Today, temperature and humidity devices are cost effective and will:
- reduce risk by detecting product exposure
- identify trends to prevent future failures
- document performance that the product was under proper control
Integrated Computer Systems
Thanks to the power of computers, the availability of product temperature database, courier delivery databases and other databases reveals a new proactive approach. This proactive approach is to process all this data from databases to improve the distribution network with new integrated computer systems.
Today computerized systems are available that integrate the shipping lane data, product condition and key gateway points onto an almost real-time dashboard. The new systems deliver to the user rapid and expanded information to make quick assessments and effective decisions. Further development of the integrated system combines the same time track with delivery data and temperature monitoring data to produce a computerized segmentation graph and chart. The integrated system is accessible via the web with protective security features. It illustrates not only product temperature but also the location of the product at any point at any given time. The integrated system will also reveal the actual shipping lane condition during the time the shipper moved through that particular location along with the alarm range for the product being shipped. Temperature monitoring data combined with delivery data can be computerized into graphic segments to:
- identify trends of potential problems that could be resolved
- identify changes in the supply chain route/shipping lane conditions
- produce documentation that confirms the product was controlled under proper conditions
In the past, the time and resources to collect information, organize data was a manual activity along with the investigation of a shipping deviation resulted in the delayed release of product(s). In many cases the investigation took at least a week and generated a resupply of the product(s) to avoid a delay of dispensing the drug to the subject, incurring additional cost.
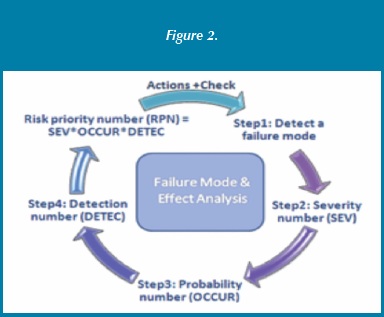
Currently, the new segmentation process has performed successfully with many of the major carriers [6] while reducing delays and promoting cost savings. When integrated computer systems have been utilized, significant productivity improvements have followed.
Detection of Risk to the Product
A common risk management tool utilized by the FDA and pharmaceutical companies for products is FMEA (failure mode and effect analysis). FMEA weighs heavily on the factor of detection. The FMEA risk priority is derived from the RPN (risk priority number) and a key factor in the RPN calculation is detectability as shown in Figure 2. Calculating the RPN for the prequalified shipper without a temperature monitor under the FMEA criteria shows a higher-risk activity. Given that a shipping container has no means of detection, the RPN value is very high compared to other options [8].
Today, we have prequalified shippers that do not use temperature monitors while claiming thermal coverage of the product during shipment in the first 72 hours. The user prepares the shipper and tracks the time of shipment to destination insuring the duration does not exceed 72 hours. If the shipper is received within the first 72 hours all is well and the product is by default released. Operationally this process makes for a clean exchange and transfer of responsibilities to the receiver of the shipper.
However, the background testing for these prequalified shippers may not adequately replicate the environment. In fact, the environment and shipper in most cases involve a high level of human intervention [4]. The amount of human intervention required to prepare and pack a pre-qualified shipper along with the unpredictable nature of the shipping lane supports the need for detection to know what happened to the product on the way to the customer.
Bottom-line: if the product is not monitored during the entire shipment, it cannot be assured that something did not go wrong during the preparation, assembly or in-transit of the product/shipper. This article should equip the user with knowledge that a great deal of risk remains when an unmonitored pre-qualified shipper system is used. Indeed, the best method of detecting product temperature for a prequalified shipper is the use of a temperature monitor.
Trends
As we look forward to the next decade, distribution will face additional challenges:
- an increase in cold chain biopharmaceuticals from 2 of Top 10 (sales) products in 2005 to 8 of Top 10 (sales) products in 2015 [1]
- quantity of temperature-controlled products will grow “roughly 8% per year (noncompounded), nearly double the 4-5% growth predicted for pharmaceutical products overall [2] ”
- there will be more supply chains for API or intermediate suppliers that will stretch across the globe and outsource distribution to an expanded network to BRICS ( an acronym for Brazil, Russia, India and China) and other emerging markets [12]
- transportation and fuel costs will be a major factor as shipment distance to customers increase [3]
- longer shipment delays will require the cold chain system to perform at a greater performance range
- a new emphasis on controlled room temperature (CRT) products [5] by agencies that will expand review of CRT products [1], introducing costly packaging to ensure thermal control [4]
Why Is This Important? – Clinical Trials Worldwide
In 2011 there were 116,868 clinical trials conducted worldwide; 80.2% of the trials were conducted in Europe and North America [11]. Over the past 5 years the number of subjects and number of studies for Phase II, III and IV worldwide have increased substantially [12]. Future trends indicate pharmaceutical products overall will have a 4-5% growth in a stagnant global economy. A major contributor to the pharmaceutical growth will come from the BRIC and emerging countries which should bring to the table a significant cost savings opportunity. However, the BRIC opportunities will require major infrastructure upgrades along with logistics and resource investments that will eventually reduce distribution risk. The benefits of these upgrades and investments will easily outweigh the distribution risks of doing business today. Since the investment and upgrades will take time, include plans that will compensate for current cost and risk.
Given time, the reduction of risk and savings as a result of temperature monitors can be substantial. For example, by cutting the shipping excursions and site temperature deviations in half, a small company with 150 clinical trials worldwide could save over $2.0M and free up at least 8 people to perform other work. In a given year, the 150 clinical trial distribution that generates over 49,000 supply shipments annually could cost approximately $35M. Furthermore, in the case of cold chain products, the distribution costs could skyrocket to over $75M due to cold chain packaging and increased fuel prices. A supplement is available for more detailed information, assumptions, calculations and comparisons [10]. The goal remains the same: ensure a quality product on time to the subject at the clinical site by the best means possible.
Summary
In summary, the best means to assure product temperature control is the temperature monitor.
Distribution is an environment continually changing with shipping containers that depend on human intervention, shipping lanes handled by different companies and unpredictable weather. The changing nature of the shipping lane, if not monitored, can affect the temperature of the product.
FMEA risk analysis considers detection of temperature, a critical factor. The prequalified shipper alone may not provide adequate temperature detection. The temperature monitor, however, offers detection of product temperature throughout the distribution shipping lane while delivering validated information as proof. In most cases, temperature monitors only provide information for one shipment.
When information is needed for one shipment a temperature monitor may be adequate; when information is needed for multiple shipments, both temperature monitors and the integrated computer system can prove to be an invaluable tool.
Unequivocally, given the trend of growth in pharmaceuticals, cold chain and CRT products, the best means to assure product temperature control at the single shipper and distribution level is the temperature monitor together with the integrated computer system.
This approach will prove what happened on the way to your customer!
References
1. Basta, N., Pharmaceutical Commerce, Nov/ Dec 2011, p.1”.
2. Basta, N., Pharmaceutical Commerce, Jan/Feb, 2012, p.26 & 30”.
3. Goff, R., “Approaches to Offset Rising Fuel and Distribution Costs” Journal of Pharmaceutical & Biopharmaceutical Contract Services”, May/June 2011, Vol. 2, Issue 3, pgs. 30-35
4. Goff, R., “Is it Worth the Risk without Temperature Monitoring” Pharmaceutical Outsourcing Journal, January/February 2011
5. Rizzo, TJ and Ulrich D., “Bringing room-temperature pharma shipping under the “CRT” umbrella” Pharmaceutical Commerce, March/April, 2012, p 22-24
6. Goff, R. Excellence Award “ COLTs- Combined Logistics and Temperature Shipping System” segmentation presentation at IQPC Europe, Rotterdam, Netherlands, 27 January 2011
7. Goff, R., “Cold Chain to Clinical site: The Shipping Excursion.” Pharmaceutical Outsourcing Journal, July/August 2008, Vol. 9, Issue 4.
8. FMEA and RPN from http://www.fmea-fmeca.com/
9. Goff, R., “Mega Scale Cold Chain Clinical Trial- A Case Study”, presentation at SMI 5th Pharmaceutical Cold Chan Conference, London, UK, 2 December 2010
10. Goff, R., Supplement to this article “Modeling the clinical trial, calculating company-wide savings and comparisons among several alternative distribution ideas” Pharmaceutical Outsourcing Journal, May/June 2012 . Based on the supplement, the distribution cost for the average clinical trial was $237,148 with investigation labor of 320 hours per study. The company-sized (group of 150 studies) distribution cost was $35,572,200 with investigation labor requiring at least 12 FTE.10 These estimates were based on status quo/existing procedures.
11. https//www.Clinictrials.gov, worldwide data search 16 January 2012 12. Hanion, Paddy, “The Evolution of the Global Supply Chain: Current Trends Altering the CTD Landscape”, Presentation at Clinical Supply Forum, Raleigh, NC, 9 February 2012 by SAI
Ray Goff has over 20 years in management with Fortune 500 biopharmaceuticals. He is a subject matter expert for cold chain, distribution, supply chain logistics, risk management and remediation. In his recent corporate role, Ray was Director, Pfizer (formerly Wyeth) Vaccines R&D leading the global clinical supply chain, logistics and distribution. Noteworthy was his successful leadership of a mega-vaccination study to over 85,000 subjects and over a hundred other clinical trials. Ray is a PMP, holds several Executive Certificates from MIT, published numerous articles and served in leadership for several associations.