Regulatory Requirements
International guidelines on Good Distribution Practice clearly stress the importance of supply chain integrity. This is first demonstrated in maintaining quality of the medicinal preparations to the final point of distribution and sales (the delivery of the product to the end user/patient), and second, in ensuring the robustness of distribution channels against the invasion of falsified medicines. The second has served as a key argument for updating the EU Good Distribution Guideline in March 2013. This article will focus on the first aspect.
USP General Chapterstates: “Drug product transport systems should be continuously monitored by calibrated monitoring systems (continuous verification), or shipping systems should be qualified and based on historical data relative to the process” [1]. This section refers to monitoring both as a method of constant verification and continuous process validation, as well as the qualification of premises and equipment. Daily inspection practices understand monitoring and qualification as two must-haves. This is in line with the WHO point of view [2].
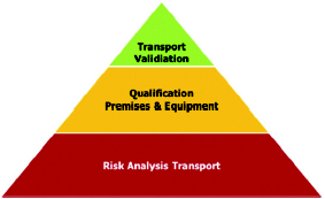
Figure 1. Process flow from Risk Analysis Transport to Transport Validation
Respecting temperature during the entire supply chain is ambitious yet fundamental to maintaining end-to-end quality of medicinal preparations, especially when degrees matter. This applies to 2-8°C products, but also to a large number of ambient and controlled room temperature (CRT) items. Maintaining the temperature corridor for the CRT products is an even greater challenge, especially when passive cooling systems are used. The unbroken temperature chain starts with the product itself, its storage conditions during transit, the transport conditions, and leads to the qualification of equipment used in this process, finally ending in a transport validation. This process is illustrated in Figure 1.
Without a solid risk analysis, subsequent steps cannot be taken. The risk analysis should follow principles provided in ICH Q9. The result of this analysis influences the extent of qualification steps: high risk, high risk priority number (full scope of qualification steps), low risk, low risk priority number (RPN), short version.
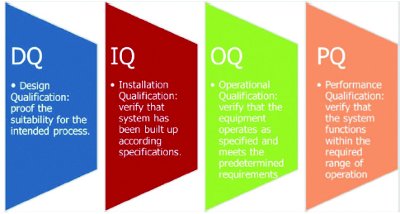
Figure 2. Qualification Process
Qualification is a key quality assurance tool in the pharmaceutical industry. Qualification proves that all premises, systems, and items of equipment work correctly and actually lead to the expected results. Qualification of storage facilities is a standard, fundamental, and accepted requirement in international guidelines. The process itself is subdivided into four segments as shown in Figure 2.
This standard process remains the same for storage facilities and equipment such as vehicles or small-scale active cooling systems (unit load devices). Applying it to the different test items remains the real challenge. For this step, guidance can be found in Chapter 4 of the most recent PDA Technical Report 64, which outlines procedures that apply to the qualification of any active-controlled system. Individual aspects and points to consider for trucks and trailers follow in Chapter 5, those for reefers in Chapter 6, and those for active ULDs in Chapter 7. Details for the qualification of storage facilities are given in the closing Chapter 8 [3]. By “qualification” PDA describes “documented testing that demonstrates, with a high degree of assurance, that a process or system function will meet predetermined acceptance criteria” [3]. Unfortunately the term “verification” is not defined in this context, though is summarized as “the evaluation of whether or not a product, service, or system complies with a regulation, requirement, specification, or imposed condition”. The focus lies on the doing, or the process of collecting this assurance.
The first stage of the qualification process is called Design Qualification. The design qualification ensures the design’s suitability for the intended process. The evaluation can comprise the following aspects:
- Process duration
- Ambient temperature
- Insulation
- Temperature control units
- Airflow in the storage compartment
- Minimum and maximum cargo load
- Monitoring devices and system (placement loggers)
- Alarm settings
The results of the design qualification and the results of the subsequent qualification steps are documented in a formal report, following documentary requirements of any GMP-activity, as shown in Figure 3.
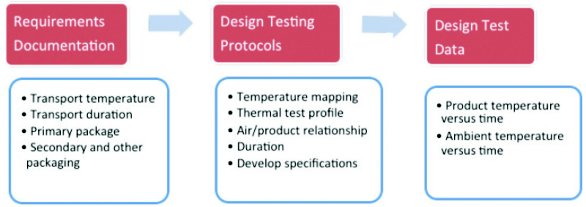
Figure 3. Design Qualification Steps according to PDA Technical Report 64 cold chain PO_
Design qualification plays a minor role in daily qualification practice. Most of the equipment to be qualified is already available and finished. The design process is finalized. Thus the qualification process starts with the Installation Qualification, incorporating some aspects of design qualification.
The purpose of the subsequent stage, Installation Qualification, is to verify that the system in question has been built up according to the specifications previously agreed upon. It leads to operational conformance. This verification can include the following four aspects:
- Document Verification – collecting relevant documentation of the system as provided by operating and maintenance manuals, spare parts lists, drawings and certifications
- Equipment Installation Verification – visual and physical inspection of the system: has the system been built up suitably? Checkpoints include: manufacturer, serial numbers, insulation, dimensions, construction quality of mounted components, general impression especially regarding hygiene and robustness
- Preventative Maintenance – design of a maintenance program based on historical data about failure and breakdown rate of critical components, parts lists with suppliers and delivery time (essential in the event of failure)
- Calibration Verification – critical devices ask for a calibration (i.e. monitoring devices that provide temperature protocols)
Operational Qualification verifies that “the process or equipment operates as specified and meets the predetermined requirements for control of the design operating parameters.” [3] The test methods should be scientifically justified, the results valid and reproducible. Operational qualification should be carried out under controlled environmental conditions. A climatic chamber is preferred for small-volume mobile refrigerating equipment. For vehicles of the “van” category, which are primarily used for last mile distribution, there are sometimes alternative possibilities for simulating ambient conditions. Halls or parts of halls that can be temperature controlled (such as food storage warehouses for low temperatures), enclosures in automobile paint shops for high temperatures, or wind tunnels at automotive manufacturers, offer alternative temperature-controlling possibilities and are the necessary size. However, these alternative simulation chambers serve merely as auxiliary tools as they differ quite obviously from qualified testing chambers. Nevertheless, they are apparently acceptable, if only when lacking other alternatives. Another option would be to qualify the testing chamber prior to the actual qualification of the vehicle. It is virtually imperative to do this if uniform temperature distribution is to be adequately substantiated. In the case of full size semi-trailers, the number of properly qualified testing chambers to choose from will be limited, and this is the real bottleneck.
The use of climatic chambers is common standard when small volume systems (insulation boxes) are tested and evaluated. Nobody would think of qualifying passive boxes without simulating temperature profiles in qualified test premises.
The ability of the system to maintain and control temperature must be demonstrated and this is the key motivation for qualifying the equipment. This is typically shown by temperature mapping studies. The distribution of the temperature over the loading space is recorded three-dimensionally. The space to be measured is subdivided into a three-dimensional chessboard pattern. Depending on the size of the loading area, 10-40 data loggers are used. Areas of temperature extremes, the cold and hot spots, are allocated. These are the ideal locations for the temperature monitoring devices. Once the ability has been verified, the following points should be considered:
- Power failure recovery testing: the recovery tests help to generate emergency plans. How long does the storage temperature in the cargo department remain within the defined temperature corridor?
- Alarm testing: verification of alarm settings and of alarm display. When, how and to whom is the alarm communicated? (Point 2 is often combined with point 1.)
- Standard Operating Procedures (SOP) verification: SOPs for operation ensure that the equipment is operated consistently with every use (loading and unloading cargo, cleaning procedures, start-up checks, preconditioning cargo compartment, alarm and contingency management).
- Temperature controls verification: test runs with different product requirements and various loading patterns, preferably executed in combination with temperature mapping studies. Modification of the temperature set points and the ability of the system to react to changing parameters should also be considered.
- Configurable parameter verification: tests of all parameters that can be configured to meet specific requirements. This test sequence is closely linked to the aspects outlined in point 4.
- Repeatability and consistency considerations: The results should clearly prove consistency and repeatability. Complete triplicate runs of winter and summer profiles are not necessary, as long as it can be demonstrated that the amount and extent of test scenarios is broad enough and results as predicted. This is a fundamentally different approach of qualification, compared to the qualification of passive controlled systems, where triplicates are indispensable.
- Acceptance criteria for the operational qualification:
a. Test runs demonstrate that the temperature control system performs as intended
b. Pertinent SOPs are listed
c. Equipment is within its calibration period
d. Cold and hot spots have been defined
e. General calibration requirements have been respected
8. Reporting criteria: general GMP-standard for written documentation have been respected, raw data cannot be altered and is available on request.
The final segment, Performance Qualification, establishes confidence that the system performs as predetermined under real conditions. A performance qualification is usually worked out in direct cooperation with the user, since customer-specific requirements predominate in this qualification phase. The challenge in this phase is the selection of the transportation routes that serve as basis for the test runs. A selection can generally be made in accordance with the following criteria:
- Maximum principal: longest transport duration
- Risk-based: route segments on which, when viewed retrospectively, a higher number of Out-of-Specification (OOS) incidents has occurred (analysis of transport logbooks)
- Maximum number of loading/unloading stations
- Different loading patterns: increasing, decreasing
In practice, making a selection certainly does not always depend entirely on one aspect or another; the selection is made on the basis of a combination of different considerations. However, first priority should be given to the risk-based selection. The performance qualification consists of a winter and summer part, in order to cover seasonal variations. The precise time of test drives in real operation is always a balancing act between attempting to cover representative, real conditions and including temperature extremes that are also likely. Actually, the only recourse here is to have a broad database, i.e. as large a number of runs as possible, made while using temperature loggers. Open door recovery is a key point to consider in last mile distribution. Imagine the high number of stops when pharmaceutical preparations are distributed from a wholesale distributor to local pharmacies. Such a transportation scenario can include 10-15 stops within a short time. At each stop, doors are opened, boxes are unloaded and empty boxes are loaded. Each time, ambient temperatures access the cargo compartment. If the recovery time for the systems is short, a strong cooling system is required. For this particular reason, vans and vehicles are often equipped with PE-curtains and/or an additional strong flow of conditioned air at the loading doors, as extra barriers.
- Maximum principal: longest transport duration
- Risk-based: route segments on which, when viewed retrospectively, a higher number of Out-of-Specification (OOS) incidents has occurred (analysis of transport logbooks)
- Maximum number of loading/unloading stations
- Different loading patterns: increasing, decreasing
In practice, making a selection certainly does not always depend entirely on one aspect or another; the selection is made on the basis of a combination of different considerations. However, first priority should be given to the risk-based selection. The performance qualification consists of a winter and summer part, in order to cover seasonal variations. The precise time of test drives in real operation is always a balancing act between attempting to cover representative, real conditions and including temperature extremes that are also likely. Actually, the only recourse here is to have a broad database, i.e. as large a number of runs as possible, made while using temperature loggers.
Open door recovery is a key point to consider in last mile distribution. Imagine the high number of stops when pharmaceutical preparations are distributed from a wholesale distributor to local pharmacies. Such a transportation scenario can include 10-15 stops within a short time. At each stop, doors are opened, boxes are unloaded and empty boxes are loaded. Each time, ambient temperatures access the cargo compartment. If the recovery time for the systems is short, a strong cooling system is required. For this particular reason, vans and vehicles are often equipped with PE-curtains and/or an additional strong flow of conditioned air at the loading doors, as extra barriers.
Additional Considerations
Temperature Mapping
Temperature mapping exercises are usually conducted during operational and/or performance qualification. It is not a regulatory requirement to do them twice. Many prefer to perform them during operational qualification, especially when test runs are executed in qualified climatic chambers. One reason for this is the availability of real cargo for the qualification process. Transport service providers normally only operate with empty boxes or dummy products.
Loading Conditions
The question is whether to use the minimum or maximum load. Though there are arguments in favor of both approaches, using the minimum load is suggested due to “increased thermal mass”, “thermal inertia” or temperature stability. Provided that loads are within the desired temperature range, increased or “full” loads represent a “bestcase” scenario”. Worst case simulation is what we are looking for. A good option would be to use vehicles with no load during operational qualification and full load during performance qualification. Only with a full load can the disruption of airflow be tested; this is a crucial element for the conditioning and maintenance of temperature.
Product versus Air Temperature
The air temperature of the cargo compartment is mapped, monitored and documented. The product temperature is the figure that decides on the final destination of the product (release, quarantine, discard). The measurement of a temperature close to the product could provide useful information especially when door openings and the recovery of the air temperature are analyzed: What is the impact of door opening on the product temperature? What is the impact on the air temperature? How long does it take for the product temperature to rise above the acceptable level when loading doors are open? These are only a few aspects that must be clarified.
Periodic Review Qualification
Processes and systems vary over the time, thus periodic reviews are necessary. Historic data can indicate trends or changes in the performance of the system. Re-qualification is required when critical parts have been altered.
Family Approach
A family approach to qualification is widely accepted. The attributes defining the system have to be clearly worked out. These attributes are “typically confirmed during installation qualification, when a determination is made that the components are similar to be treated as a family. This approach enables manufactures to lease equipment in a clearly defined family from different suppliers at different times and still operate within the qualified parameters”.
Closing Remarks
Equipment provides the required assurance level for the safe transport of temperature-sensitive pharmaceutical products in qualifying vehicles and vans. It is one essential ingredient of the integrity of the supply chain. Other factors such as transport validation and proper training of involved staff members are of equal importance. Working on standard test profiles is a future challenge. Standard test profiles help to evaluate the performance of different systems. A draft of such a short profile may show the following characteristics: 4-hour test duration, +35°C and -5°C ambient temperature, 12 door openings, without any load.
References
- Unites States Pharmacopeia (USP), 36, Chapter 1079, page 5.
- Chapter 6 “Transport and Delivery”, World Health Organization. WHO Technical Report Series, No. 961, 2011 Annex 9. “Model guidance for the storage and transport of time- and temperature–sensitive pharmaceutical products”.
- PDA Technical Report 64, Active Temperature-controlled Systems: Qualification Guidance, 2013.
Dr. Nicola Spiggelkötter is an independent management consultant focusing on pharmalogistics and strategy consulting. Qualification, validation, auditing services, trainings as well as implementation and adjustment of quality systems are in the realm of expertise covered by her consultancy. Dr. Spiggelkötter holds lectureships in Germany and abroad. She is a frequently invited speaker and can be reached via e-mail at: [email protected]