Abstract
Critical design parameters of trailer equipment and operational handling procedures in road transportation have a major impact to the airflow and temperature distribution within temperature controlled road vehicles. Within Europe, ATP FRC certified 13.6 meter long mono- and bi-temp trailers are the most common vehicles for domestic and international temperature controlled distribution. Each trailer has a mounted temperature controlled unit (TCU) at the front to generate enforced temperature controlled air circulation in the cargo space. The bi-temp trailer has in addition a second evaporator attached to the ceiling at the rear doors and a movable split wall that can divide the trailer cargo space at various positions to maintain different temperature regimes. Under the leadership of the Pharmaceutical Cold Chain Interest Group (PCCIG), global subject matter experts collected 72 requirements towards trailer equipment and operational handling to distribute pharmaceutical products at +2 °C to +8 °C and/or at +15 °C to +25 °C in these vehicles. By applying the collected requirements and guidance for FTL (Full Truck Load) and LTL (Less Than Truck Load) networks, the pharmaceutical industry and its supply chain partners can harmonize trailer equipment and operational handling. This will improve services and reduce cost and temperature excursions across the supply chains for temperature controlled road vehicles. Presented requirements may be found applicable to other temperature controlled road vehicle types and sizes as well including the shorter temperature controlled trailers of 8 to 11 meter long.
Keywords
Temperature controlled trailers, mono-temp trailer, bi-temp trailer, requirements, qualification, temperature controlled unit, ATP FRC certification, movable split wall.
Introduction
Within the pharmaceutical industry each company has defined its own set of requirements for temperature controlled trucking of their temperature sensitive products at +2 °C to +8 °C and/or +15 °C to +25 °C. These requirements are the result of best practices and executed qualification studies with fully loaded, partially loaded and/or empty vehicles under summer and/or winter conditions (hot and/or cold temperature profiles). With the publication of the revised EU GDP guidance in 20131 and EU GMP Annex 15 in 2015,2 many pharmaceutical companies and wholesalers were required to execute qualification studies and to deliver a set of data for temperature controlled vehicles. As each company followed its own approach, different studies were set up that resulted in different requirements. As a result, forwarders, carriers and drivers have difficult times to align all customer requirements for LTL transportation, which can impact product services, product quality, safety and efficacy.
The PCCIG of the Parenteral Drug Association (PDA) recognized that the pharma industry, wholesalers, forwarders and carriers should collaborate to align temperature controlled trucking requirements in order to improve operational handling, avoid temperature excursions, and reduce cost. Therefore a global team of subject matter experts was formed to develop a set of requirements for operational handling of products with shipping conditions at +2 °C to +8 °C and/or +15 °C to +25 °C based on best industry practices, qualification studies, and to share the proposed information with all supply chain partners.
A temperature-controlled trailer is defined in PDA Technical Report 643 as a cargo box attached to a truck that is equipped with a temperature controlled unit (TCU) to provide active cooling or heating control inside the box (see Figure 1). The TCU is sometimes called the reefer unit. For this article the team scoped temperature controlled trucking to only ATP FRC certified4 temperature controlled trailers with an external length of 13.6 meters operating with one TCU (so called mono-temp trailer) or with one TCU mounted at the front of the trailer and a second evaporator at the rear doors (so-called bi-temp trailer). These are the most common temperature controlled road vehicles in domestic and international road transport within Europe to keep temperatures at +2 °C to +8 °C and +15 °C to +25 °C. The bi-temp trailer has a movable split wall that can divide the front from the back of the trailer. The evaporator at the rear doors controls the temperature in the rear section. Freezer products, non-temperature controlled trucks and trailers, vans, qualification of trailers and positioning of additional temperature loggers by shippers are not within the scope of this document. Qualification is excluded as this topic is discussed in many other references (see references 1-10).
Figure 1. Schematic drawings of a loaded mono-temp trailer (top left) and bi-temp trailers with two compartments (top right and bottom). The arrows in the drawings indicate the airflow directions inside the trailers. Tables 2 and 3 provide further guidance in ensuring and maintaining airflow within the cargo space.Risk in Temperature Controlled Road Transportation
Before setting requirements regarding temperature controlled trailers and operation handling, one should be aware of the risk of temperature excursions related to equipment, external factors, processes and people (see PDA Technical Report 58 for additional reading, ref. 5). Table 1 lists a few risks that may lead to temperature excursions. These were taken into account during the collection of the requirements.
Table 1. Risk of temperature excursions due to equipment, external factors, processes and people.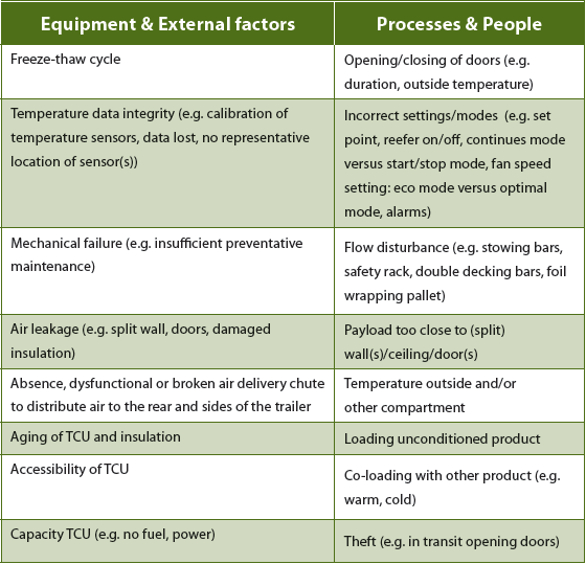
The knowledge about the differences in operational handling of monotemp and bi-temp trailers is important. Compared to mono-temp trailers, the use of bi-temp trailers has economic advantages:
- Fuel reduction when split wall is down with less than full load in the front compartment.
- Transportation at two temperature ranges resulting in better utilization of cargo space.
On the other hand, complexity and elevated risk to temperature excursions are added to temperature controlled trucking when using bi-temp trailers:
- Multiple set point settings.
- Careful planning (un)loading sequences.
- Reduced and different airflow in the rear compartment due to absence of bulk head and limited TCU capacity at the rear doors.
As a result, the use of bi-temp trailers is related to more risks than monotemp trailers and clear requirements must be set to avoid temperature excursions and to optimize operational handling.
Selection of Temperature Controlled Trailers
The 13.6 meter long ATP FRC certified monoand bi-temp trailers have insulated ceiling, floor, walls and doors with a standard external length of 13.62 meter and usable internal dimensions of approximately 13.32 meter length, 2.46-2.50 meter width and 2.50-2.75 meter height. Both trailer types have a mounted TCU at the front, while the bi-temp trailer has connected to the main front TCU a second evaporator attached to the ceiling at the rear doors. In PDA Technical Report 64,3 six critical design parameters are defined that have an impact on the temperature distribution inside the cargo space. These parameters include heat exchange energy, airflow, insulation, thermal integrity, temperature monitoring system and alarms. In Table 2 the pharma requirements for mono- and bi-temp trailers and their rationale are listed using the critical design parameters as starting point.
Operational Handling
A quality management system (QMS) should be in place to ensure that each step during operational handling in the transport process is executed according to the designed and qualified process. In addition to the QMS, seven other categories are defined for temperature controlled trucking as defined in Figure 2 including maintenance of trailers, planning of the shipment, payload preparation, trailer inspection prior loading, loading of payload, transport and unloading of the payload.
Figure 2. Categorization of operational handling for temperature controlled trucking.Table 3 lists the collected requirements brought forward by the authors for the operational handling of mono- and bi-temp trailers. The requirement numbering from Table 2 is continued in Table 3.
Table 2. Trailer equipment requirements and their rationale for mono- and bi-temp trailers.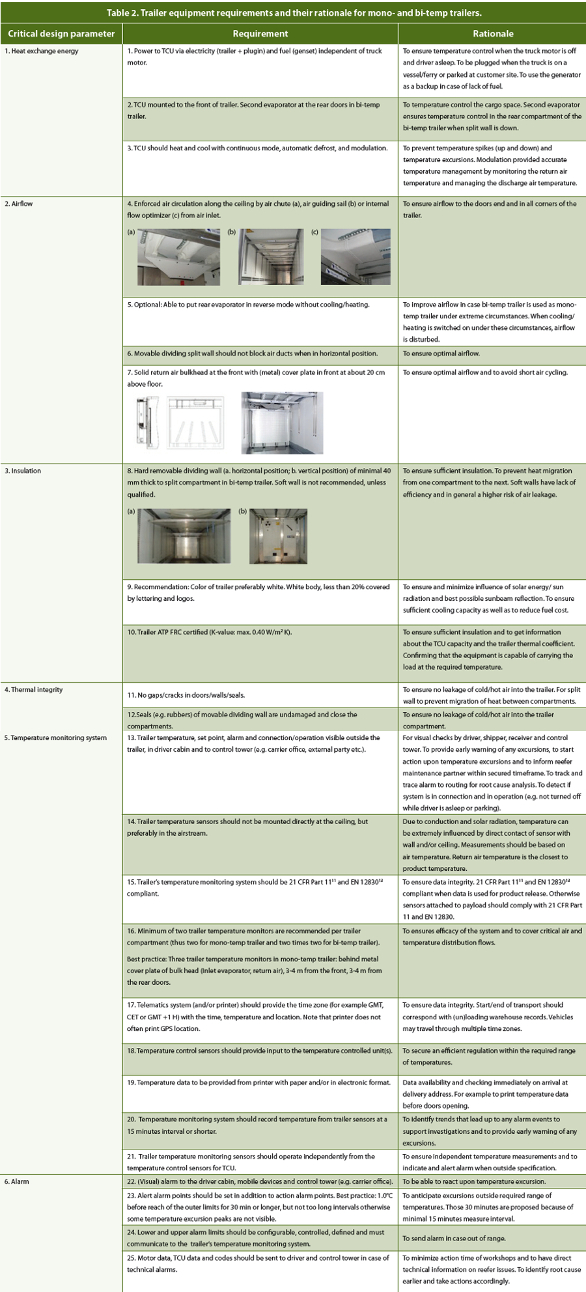
Table 3. Operational handling requirements and their rationale for mono- and bi-temp trailers.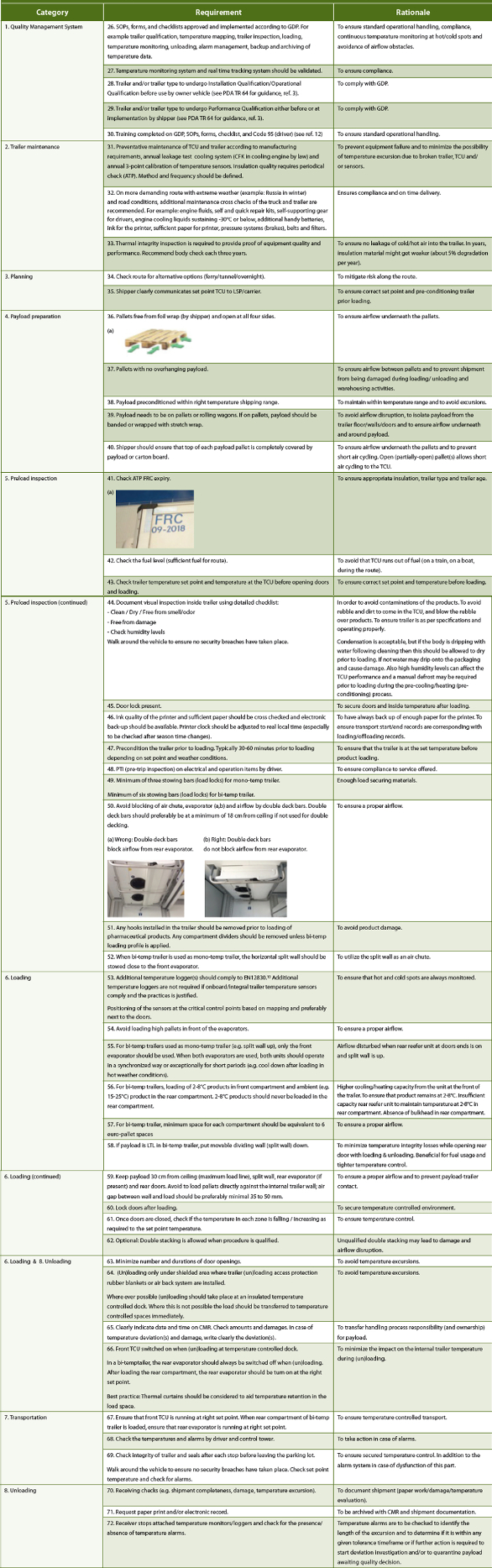
Discussion
For shipping temperature controlled pharmaceuticals, trailers designed and maintained according to applicable standards and qualified according to industry best practices (as suggested in PDA Technical Report 64) are required. There is a relative lower risk on temperature excursions when only dedicated monotemp trailers are used for FTL transport when these are loaded correctly. However when bitemp trailers in a LTL network are used in combination with a cross-dock, the risk on temperature excursions increases due to the added complexity in handling process and shipping lane. On the other hand the transport cost and CO2 emissions will decrease due to better trailer utilization in a LTL network. Table 4 provides an overview of these differences. It is up to the shipper and/or paying party to decide which (hybrid) model should be applied. This is depending on the product characteristics in combination with the acceptable associated risks and user requirements.
Table 4. Differences in using FTL and LTL networks in temperature controlled road transportation.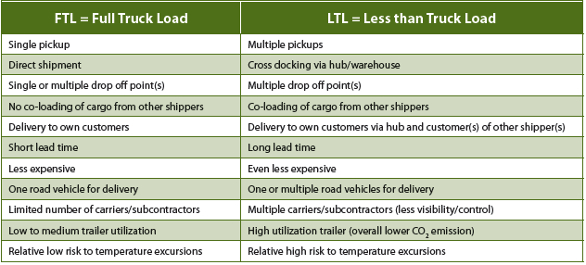
In the recent years shorter temperature controlled trailers of about 8 to 11 meters long appeared in the market. These so-called city trailers are mainly used in domestic distribution in and between urban areas. The requirements developed for the 13.6 meter long ATP FRC certified temperature controlled trailers can also be applied to these shorter temperature controlled trailers.
Conclusion
Any airflow disruption and deviation from requirements can increase the risk of temperature excursions during temperature controlled trucking. Therefore all efforts discussed above should be taken into consideration to ensure the usage of proper equipment and execution of operational handling procedures based on the established requirements. By applying the collected requirements and guidance to FTL/ LTL transports, the pharmaceutical industry and its supply chain partners can harmonize equipment utilization and operational handling. This will improve services and reduce cost and temperature excursions across the supply chain. Presented requirements may be found applicable to other temperature controlled road vehicle types and sizes as well including the shorter temperature controlled trailers of 8 to 11 meters.
References
- European Commission: Guidelines on Good Distribution Practice of medicinal products for human use, 2013/C 343/01, November 2013.
- European Commission, Directorate – General for Health and Food Safety: EudraLex Volume 4, EU Guidelines for, Good Manufacturing Practice for Medicinal Products for Human and Veterinary Use, Annex 15: Qualification and Validation, March 2015.
- Parenteral Drug Association, Technical Report No. 64 (TR 64) - Active Temperature-Controlled Systems: Qualification Guidance, October 2013.
- UNECE - Agreement on the International Carriage of Perishable Foodstuffs and on the Special Equipment to be Used for such Carriage (ATP), 2016.
- PDA Technical Report No. 58 (TR 58): Risk Management for Temperature Controlled Distribution, September 2012.
- USP 39–NF 34.Good Storage and Distribution Practices for Drug Products, Rockville, MD: United States Pharmacopeial Convention; 2016.
- HPRA IA-G0011-1: Guide to Control and Monitoring of Storage and Transportation Temperature Conditions for Medicinal Products and Active Substances, 2011.
- WHO: Qualification of temperature controlled road vehicles, January 2014, Technical supplement to WHO Technical Report Series, No. 961, 2011.
- DIN SPEC 91323. Temperature conditioned transport equipment used for the distribution of pharmaceutical products (for human beings or veterinary use) – Guidelines for qualification, 2016.
- IATA TCR (Temperature Control Regulation) 5th edition, 2017, Section 17.8.1.1 Road Feeder Service (RFS)
- Electronic Code of Federal Regulations (e-CFR): Title 21: Food and Drugs PART 11 - ELECTRONIC RECORDS; ELECTRONIC SIGNATURES
- DIRECTIVE 2003/59/EC OF THE EUROPEAN PARLIAMENT AND OF THE COUNCIL of 15 July 2003 on the initial qualification and periodic training of drivers of certain road vehicles for the carriage of goods or passengers, amending Council Regulation (EEC) No 3820/85 and Council Directive 91/439/EEC and repealing Council Directive 76/914/EEC
- EN 12830: Temperature recorders for the transport, storage and distribution of chilled, frozen, deep-frozen/ quick-frozen food and ice cream - Tests, performance, suitability
Disclaimer
The content and the view expressed in this document are the result of a consensus achieved by the authors and are not necessarily views of the organizations they present or represented.