Providing customers with their order when they want it, at the right price and quantity, is only laying the foundation for excellent customer service. Mitigating risk through planning and rapidly responding to unexpected events are also essential. Teamwork and collaboration, both within a CDMO and with customers, combined with a lean quality management system, ensure the highest levels of customer service.
DEFINING A HIGH LEVEL OF CUSTOMER SERVICE
At the beginning of each new project, a CDMO works alongside its customer to set milestones that enable the customer to meet specific project timelines. To provide the highest level of customer service, the CDMO must be able to meet each of those milestones on time and to the expectations of the customer for quality, quantity and price. This requires the CDMO to have a thorough understanding of the project, its complexity and any inherent risks. The CDMO must also have the capability to develop a remediation plan to ideally eliminate, or otherwise reduce, those risks.
Projects do not often exactly follow the plan. To achieve a high level of customer service it is necessary to provide customers with what they expect, despite being faced with unexpected challenges. Whether the issue originates on the customer’s end or at the CDMO, having the ability to quickly resolve problems is paramount.
In this regard, flexibility is also essential. Market dynamics are fluid and situations often change. For instance, unexpected demand increases can occur. While a good problem to have, such increases require a contract manufacturing partner with flexible capacity to act as an extension of the customer and meet that need.
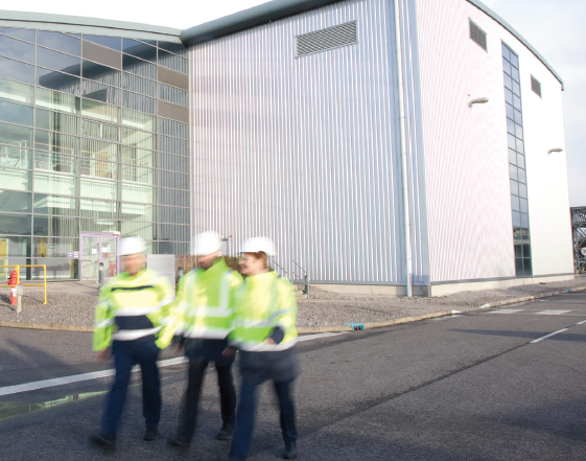
LEAN QUALITY MANAGEMENT IN THE PHARMA INDUSTRY
In recent years, cost pressures have continued to increase and evidenced-based and personalized medicine has begun to drive expectations for accelerated development of next-generation treatments, breakthrough therapies and orphan drugs. There has also been an increase in the number of 483s — citations for non-conformity/non-compliance with pharmaceutical regulations — issued by the US FDA.1
Consequently, drug manufacturers are seeking new approaches that facilitate drug development and manufacturing while maintaining high quality. Many have found that Six Sigma aligns well with the reduction of variability, a main goal of regulatory agencies.2 Lean manufacturing has also been introduced, with most efforts initially excluding quality programs for fear that quality performance would be reduced.3 Lean principles have since been applied to improve quality control programs without impacting process and product quality, but these first initiatives kept quality programs separate from other company operations.
Manufacturers have realized, however, that incorporating quality into operational excellence programs leads to greater improvement. Such holistic, lean quality management platforms “strive for the ‘perfect’ end-to-end state, where value and responsiveness to the customer are maximized, and waste and delays are eradicated throughout the entire value chain.”3 Effective lean quality management systems enable pharmaceutical companies to balance operational efficiency with regulatory compliance, helping to ensure that quality programs and processes control and support, rather than constrain, drug development and manufacturing.
The results can be significant. Lean quality management systems that are validated to Good Manufacturing Practice guidelines and thus standardized, transparent (visual) and closely measured, when implemented by an experienced team, can lead to improved compliance, greater process and product quality and enhanced customer service.1
TRUST IS THE BASIS OF LEAN QUALITY MANAGEMENT
There are various elements to a lean quality management system, such as supplier, customer and regulatory audits, investigation of issues and thorough documentation, to name a few. Unlike these program components, however, the most important element — trust — is intangible. A customer must be able to trust that its CDMO partner will meet its expectations. To do so, the CDMO must have an effective team that can execute and manage its lean quality systems.
Such a team must be composed of highly experienced and qualified individuals. With multiple sites producing drug substances and drug products, Avara Pharmaceuticals has many people with different knowledge bases and areas of expertise creating a network of subject matter experts. Rather than duplicate positions at each site, we capitalize on the passions and experiences of our people to support the various elements of our lean quality management system.
The team meets regularly and collaborates to develop a quality system that is consistent and effective across the entire Avara network. They also spend time in the quality control laboratories and on the production floor conducting visual management evaluations, not only as a management team but with company executives and customers, to look at all elements of the quality system. Such a dynamic approach and our striving for continuous improvement ensure that we not only meet our customers’ expectations and regulatory requirements, but that we continue to deliver the best results.
This consistent approach is also essential to facilitate trust building with our customers, who expect one quality system across our network. That includes one document system, one approach to investigating issues and one regulatory compliance approach at our API and finished-dosage manufacturing facilities.
MANAGING CULTURAL DIVERSITY AND RESISTANCE TO CHANGE
Bringing disparate sites together to form a new company can be challenging. Each facility has its own culture and legacy systems, including quality management initiatives. At Avara, we have taken great care to be sensitive to cultural differences while we collaborate to develop an effective global lean quality management system. Our experts across all of our different sites are not only willing to come together, but to listen and challenge each other to ensure real understanding of all possible approaches with the goal of identifying the most efficient and effective ways of working.
This network approach is also essential for overcoming resistance to change. Moving to new quality systems can be particularly difficult for people who have only worked at one facility and only have one experience with quality management. Creating an effective lean quality management system helps overcome this resistance to change.
With sites that are new to the Avara network, existing procedures are employed initially and the site is gradually converted to our quality system. People with experience, skills and real passion are brought into the expert network to help with integration.
As an example, many sites have their own information technology systems — often locally modified versions of common software such as SAP, Empower and Labvantage — that must be migrated to Avara’s systems. In general, most pharmaceutical manufacturing sites are familiar with programs such as Empower, thus switching is a matter of upgrading from one version to another. It is more challenging to convert new sites that have mostly manual processes to Avara’s automated solution or to convert a documentation system to Avara’s customized module, because in these cases people must change the way they work. Helping make these changes is crucial to introducing leaner ways of thinking and working.
Again, honesty and openness are crucial. Communicating our expectations to people as quickly as possible helps them understand what is needed and also creates trust. People appreciate that we are genuinely interested in their opinions. We listen to all ideas and choose the best possible solutions. This approach also allows us to identify people that are passionate about quality and want to take an active role, so they can be incorporated into our expert community.
LOCAL TO GLOBAL APPROACH
Quality issues typically occur on the local level, but Avara takes a global approach to addressing them. When an issue or event occurs at one Avara facility, the problem is thoroughly investigated and resolved at the site, with the knowledge then applied across the Avara network.
This combined local and global approach guarantees that effective solutions are applied across the Avara network, even before issues can arise at other facilities.
THE GREATEST ASSET
Ultimately, we realize that what we do at Avara will impact the lives of people we will never know. We value employees with passion, drive and a desire to help implement a lean quality management system that allows us to revolutionize the industry by focusing on our people, our customers and the patients we ultimately serve.
As a result, we believe that our people are our greatest asset. We treat them fairly. We want them to be properly trained in all aspects of their jobs and informed and educated about the industry, as well as what Avara is doing. They, in turn, understand the importance of doing the right things right, every time, and the potential implications when they don’t. We have a high-quality standard, and our employees ensure that we maintain it. They recognize the importance of being partners with our clients and that by providing the highest level of customer service we are in turn serving the patients that rely on the medicines we produce.
REFERENCES
- Julia Holmes. “How Can Lean Support Quality And Compliance In Pharma?” Lean Coaching. 18 Feb. 2014. Web.
- Laura Smith. “The Six Sigma Cure.” Quality Digest. Mar. 2006. Web.
- “Adding Value With Lean Quality.” Tefen Management Consulting. Web.
ABOUT THE AUTHOR
Warren Horton
Executive Vice President Global Quality Assurance and Regulatory Affairs, Avara Pharmaceutical Services
Warren has 35 years of industry experience with a broad pharmaceutical background and extensive experience in manufacturing management, quality assurance, quality control and operational excellence. He joined Abbott Laboratories and the pharmaceutical industry in 1986 and has had successive levels of leadership and responsibility in manufacturing and quality assurance. Warren has experience in new plant start-ups, remediation of consent decrees and warning letters, quality system integration and data integrity remediation.
LinkedIn www.linkedin.com/in/warren-horton-5154444