What are some of the current critical issues facing the industry in regards to oral solid dosage manufacturing?
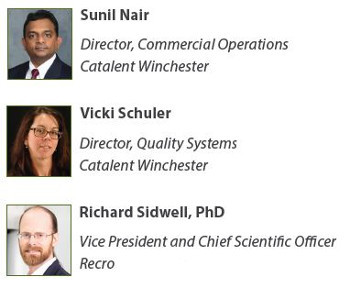
Sunil Nair, Director, Commercial Operations, Catalent Winchester and Vicki Schuler, Director, Quality Systems, Catalent Winchester: Many issues that the pharmaceutical drug development industry face not only affect oral solid dose manufacturing and one of the constant challenges is the scalability of new molecules emerging from the drug development pipeline. Successfully replicating bioavailability and the effectiveness of the drug product at commercial scale through a viable, repeatable and sustainable process is key. Another challenge is the rising pressure of cost, which drives for shorter timelines to deliver the right solution, whilst not compromising on quality and compliance. In this extremely dynamic environment, speed is becoming the routine expectation, and global competition to provide such efficiency is increasing. Today, there are fewer blockbusters, and more start-up and virtual companies with less in-house resources, so a development and manufacturing partner must be flexible and constantly innovate and deliver to meet the demands of its customers, and ultimately, the payers and regulators.
Richard Sidwell, Ph.D., Vice President and Chief Scientific Officer, Recro: There are many critical issues facing oral solid dosage manufacturing, just as for other pharmaceutical products. Two that seem to be cropping up more often at the moment are globalization of the supply chain and data integrity. The large number of globally distributed suppliers, while helpful from a cost perspective, is making quality oversight much more difficult. At the same time, particularly in the early phases where individual shipments of material can easily show up on the critical path, shipping lead times and import/export requirements often create uncertainty and delay. Similarly, the promise of efficiency gains through digitization and automation are being offset by the frontloaded difficulty and effort needed to ensure security, integrity, and validation of those systems. As expectations continue to rise for scientific depth (and massive amounts of data) in development, these challenges must be met.
Can you tell us about some new oral solid dosage manufacturing technologies and/or processes that are helping pharmaceutical companies bring new products to market or are reviving older products?
Nair and Schuler: Pharmaceutical manufacturers are constantly deploying technologies that aim to improve the bioavailability of drug products and help manage or extend product life cycles. One of the noteworthy areas gaining attention is spray drying, which is a continuous process that converts a liquid feed into a powder, and is ideal when particle size, morphology and stability need to be controlled. Additionally, the use of roller compaction for dry granulation is a technology that is increasingly popular for poorly flowing APIs, and formulations where content uniformity can be a challenge.
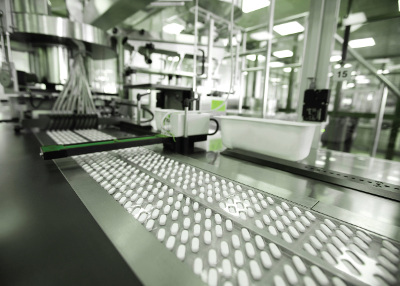
Catalent’s expertise in the areas of modified- and controlled drug release offer multiple options to pharmaceutical developers. Catalent’s Zydis® ODT (orally disintegrating technology) is an oral solid dosage form that disperses almost instantly in the mouth, with no water required. It is well suited for line extension initiatives, and a good option for delivery to pediatric and geriatric patient populations.
When a pharmaceutical company is choosing an oral solid dosage manufacturing/service provider, what questions should they ask? What qualities and expertise should an oral solid dosage manufacturing/service provider have to ensure that their client gets the best quality product?
Nair and Schuler: First, sponsors should evaluate the provider’s track record of successfully delivering results in a compliant manner. There are five C’s to consider as part of a standard evaluation criteria: capability, compliance, capacity, customer service and cost. At Catalent, these factors are constantly challenged through internal bench-marking to standards that meet and exceed industry standards. As a company, we are guided by a ‘Patient First’ philosophy that nurtures a culture of innovation and responsible decision-making. This also helps us attract and retain the best talent in every area of our workforce. Catalent’s global scale, with over 35 sites, provides the options at each stage and scale of manufacturing, including redundancy, to ensure supply continuity.
Other than expertise in managing current and future technologies, providing innovative solutions that are timely and less expensive creates differentiation from competitors. Customers are looking for stability, appetite for partnering, and a partner company that can provide a return on their investments.
Sidwell: When choosing a CDMO for oral solid dosage development or manufacturing, there are a few key questions to ask. They generally fall in the areas of quality, track record, and capability. If quality systems are not sufficient in the early stages, you will be building on a shaky foundation. This will sometimes show up in the company’s track record. Are there warning letters in their recent history? Have they successfully completed similar projects for others? Have they ever supported a product like yours all the way to FDA approval? Next, consider their capabilities. Are they capable of supporting your product with the right equipment and expertise, not just now, but also for the next scale of your project? If you are satisfied with all of these points, one final thing to consider is whether the size and culture of the business is a match to yours. Are they big enough to really support you, small enough that your project will really matter to them, and do you trust the team will be steady and good to work with? If you plan for success, you will be working together for years.
How has the globalization of the pharmaceutical industry affected oral solid dosage manufacturing? How do you ensure that products manufactured meet individual country regulations?
Nair and Schuler: The pharmaceutical supply chain network has become increasingly complex with API manufacturing, formulation development, dose manufacturing, packaging, and distribution all needing to be designed with the global market in mind. While on one hand there is a need to consolidate operations to gain economies of scale, the challenge is also adhering to the regulatory requirements of individual countries and regions. More recent events like “Brexit” and the associated uncertainty impacting drug manufacturing and distribution within and outside the EU poses peculiar challenges by itself. Innovation, and providing creative solutions that are timely and less expensive, is essential to create differentiation from competition.
The challenge to remain in compliance with country-specific legal and regulatory requirements is continually increasing as pharmaceutical manufacturing becomes more globally competitive. Partnering contract manufacturing organizations can develop a market advantage because they can carefully assess the ability to comply with specific country manufacturing requirements before committing to manufacture product for marketing in any country. This is achieved through monitoring via regulatory intelligence and discussions with customers. In addition, routine internal auditing programs help maintain compliance and help provide a competitive advantage to react to regulatory changes, industry expectations and global compliance initiatives such as data integrity and prevention measures for cross contamination. Although this often requires investment of time and capital, with compliance and quality teams working in close partnership with engineering and operations teams, the value to meet patient safety expectations globally is a requirement of most customers.
What do you see as the future of the oral solid dosage manufacturing?
Nair and Schuler: Due to the increasing number of large molecule drugs, oral solid dosage manufacturers need to focus their efforts on treatments being developed that address unmet medical conditions in areas of serious, life-threatening diseases (i.e., orphan drugs, highly potent compounds, etc.). Technological innovations for pharmaceutical processing and product development will be the focus areas for many pharmaceutical developers looking for a formulation and manufacturing service provider that can provide expertise and capabilities with customized solutions.
It is imperative that manufacturers design their processes to be highly efficient. Adopting newer models like continuous manufacturing can introduce efficiency at smaller scales, as opposed to traditional batch manufacturing processes. Innovation, flexibility and providing tailored solutions to customers will be a key requirement.