Tablet press design innovation has traditionally centered on largescale production equipment, however, there is increasing focus on the smaller-scale, mid-range models that must have the capability to support product development, scale-up, tech transfer, clinical batch manufacturing, small and medium batch production, and continuous manufacturing applications. This range of capabilities demands unique features and design flexibility.
A small-scale press must have the capability to work with a wide range of material quantities, from just 1 kg or less to batch sizes up to 50 or 100 kg. This requires the press control system to work effectively with a reduced tools configuration, where press tools are installed in every second or third station in the turret. This reduction of tools permits flexible operation with reduced material quantities and minimizes tooling investment in the development phase. Options to reduce the volume of the feeder are also required, including reduced volume feeder paddles, or a gravity feeder.
Small-scale presses must offer a comprehensive instrumentation package to permit real-time measurement and display of precompression force, main compression force, and ejection force. For bi-layer operation, the first layer tamping force also is a critical point of instrumentation. For product development, the press should have an on-board data acquisition and analysis capability that will collect high-speed data (press force versus time) and provide automated analysis to characterize force peaks, rate of force application, rate of force decay, area under the compression curve, and contact time. These parameters permit formulations to be assessed, optimized, and compared to established baselines.
Most small-scale presses are asked to do many things – so flexibility is paramount. Many applications require a single and bi-layer capability, and a fast-change conversion process that can be managed by the user directly. In combination with an exchangeable turret capability, the press can then produce a tablet of any size and shape, in a single or bi-layer format. A mixed turret, which includes both B and D punch bores and dies on the same pitch circle, provides the same flexibility in a reduced tools configuration, and without the need to execute a turret exchange. Finally, a small-scale press should offer some level of portability to accommodate those facilities where a dedicated room cannot be made available.
For small and medium size batch production, the ability to move quickly from batch to batch and product to product is a key consideration. If the press is being cleaned and retooled more often than it is running, which is often the case with older tablet press technology, the resulting efficiencies are extremely low. To facilitate a fast changeover, there are two key components that should be considered. First, an exchangeable turret, fully tooled off-line and ready to go, will dramatically reduce changeover times, while maximizing output for each product. For example, a small-scale press may offer a range of turrets, as follows:
For a production portfolio that includes a wide range of tablet sizes, from 8 – 22 mm, for example, a single turret strategy would require the TSM or EU D turret, with 23-stations. While this turret would accommodate all tablet sizes, employing a multiple turret strategy would permit output gains for the smaller tablets, as follows:
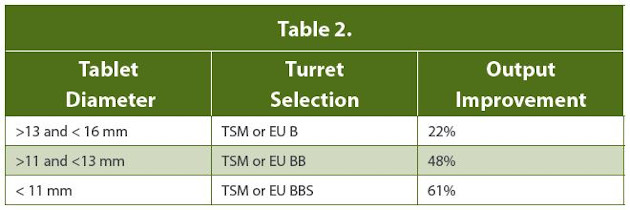
In addition to efficiency gains that may be realized from a robust turret exchange strategy, the use of fast change parts can also represent a significant opportunity to implement efficiency improvements. A well designed, small-scale press will have minimum parts to remove to facilitate a turret exchange, and smooth surfaces with good accessibility to clean the compression zone. Having a second set of product contact parts, including the feed hopper, feed pipe, feed frame, tablet take-off, and discharge chute – cleaned and ready to go – will streamline the changeover process. A parts cart, designed to ensure the repeatable position and placement of the product contact parts during disassembly and assembly, can also boost changeover efficiency.
Subscribe to our e-Newsletters
Stay up to date with the latest news, articles, and events. Plus, get special offers
from Pharmaceutical Outsourcing – all delivered right to your inbox! Sign up now!
As product containment becomes an increasing focus for tablet compression equipment, small-scale machines must offer comparable containment solutions. For medium containment requirements, an OEB 3 solution, which conforms to an OEL (Operator Exposure Level) of 10 – 100 μg/m3, is most appropriate. Typical enhancements for OEB 3 containment include improved windows seals, tri-clamp connections for incoming material, and tri-clamp connections on the discharge chute outlets to permit contained transfer and collection of samples and tablet rejects. In addition, the compression zone should be configured with a differential pressure sensor that permits the measurement of negative pressure in the compression zone, which is then established as a run permissive. An inlet HEPA filter prevents any blowback to the room, in the event that there is an interruption of negative pressure, and more advanced systems may be configured with a motorized damper and a contained air handling unit, which will allow negative pressure in the compression zone to be controlled to a predetermined setpoint.
In addition, a split discharge chute design, in which the discharge chute is terminated in the compression zone and a transfer segment is mounted to the press window, ensures the contained transfer of tablets from the press. To permit contained access to the compression zone and facilitate manual intervention during operation, the windows of the press should be configured with interlocked glove ports and an RTP (Rapid Transfer Port) that lets press tools or small hand tools to be passed in and out of the compression zone without breaking containment. A manual vacuum wand in the compression zone, manipulated via the glove ports, allows the press zone to be cleaned before a manual mist can be applied to bind the airborne particulate. In most cases, PPE will be required to complete the cleaning process.
For higher levels of containment, including OEB 4 (1 – 10 μg/m3) and OEB 5 < 1 μg/m3), a full Wash-In-Place (WIP) execution with integrated isolator is required. This system also requires many of the same features as the OEB 3 execution, including tri-clamps and negative pressure control, but is further enhanced by the use of 316L stainless steel components and water-proof electrical components suitable for the wash-in-place environment. A WIP skid, which can provide heated water with multiple detergent options, is often employed, and the WIP recipe is established and executed via the tablet press control system.
For all containment solutions, an integrated approach is required in which the complete system – consisting of the press, deduster, metal check, tablet tester, containment valves, WIP skid and air handling system – is integrated with all make-break connections and valves and, for operation ease, managed from a single HMI.
For utilization in a batch production mode, for clinical manufacturing or small to medium batch sizes, the small-scale tablet press must have a full production-scale control system. This means secure operator login and authentication, electronic audit trails to track machine adjustments, alarms, and tablet rejects, as well as secure batch data handling to ensure full compliance with 21 CFR Part 11. A press force control system, which permits automatic tablet weight control by monitoring the compression force and making precise adjustments to the dosing cam, also is a critical requirement of the small-scale press control system. The press force control system must also facilitate automatic layer weight control when operating in bi-layer mode. A single tablet rejection capability, based on the monitoring of individual press force values, will reject and record the punch station of every rejected tablet over the course of the batch, as well as identify problematic tool stations.
For a higher level of automation, the press control system should permit a seamless interface to peripheral devices surrounding the machine, including an overhead feed system or post hoist, tablet deduster, metal check, tablet diverter, tablet collection system, or inline tablet tester, which will automatically sample and measure tablet weight, thickness, and hardness in real time. Finally, the control system must offer a network integration capability to support product recipe management, secure batch data storage, and the transfer of process data to a central SCADA system or historian.
The use of Industry 4.0-capable sensors and the integration of onboard diagnostics is also critical, especially in product development settings where immediate maintenance support may be limited. Another key feature for the small-scale press is a control system HMI with on-board help, including access to manuals, electrical schematics, spare parts lists, assembly drawings, work instructions, and procedural videos to support the machine setup, turret exchange, and machine changeover.
The small-scale tablet press is generally the machine of choice for continuous manufacturing applications, as the output capability aligns with typical process requirements. For this special application, the press should permit the integration of NIR or RAMAN sensors to yield real time, in-line measurement of content uniformity. These sensors are often placed in the material feed pipe or, preferably, directly in the feeder where the dies are filled. These sensors provide feedback to the supervisory control system, which may then access the tablet press control system to direct the flow of tablets to the good or reject channel. The supervisory control system should also be able to download product recipes and make in-process adjustments to the dosing cam or tablet thickness settings while the machine is in operation. Success in a continuous manufacturing line requires an open control system architecture that supports seamless integration of the tablet press to the central, supervisory control system.
Given the many ways that small-scale tablet presses are required to operate, it is clear that sophisticated technology is required – to ensure that the press has the flexibility and capability to work effectively and efficiently in a diverse range of production environments and applications.
Author Biography
Frederick Murray, President of KORSCH America Inc., a leader in tablet press technology offering solutions for product development, scale-up, high-speed production, multi-layer, mini-tablet, and WIP/high-containment applications. www.korsch.com