Erik J. van Asselt, PhD - MSD; Janusz Mielewczyk – Amgen; Rafik H. Bishara, PhD - Technical Advisor; Zvonimir Majic, PhD - TEVA Pharmaceutical Industries Ltd.; Volker Cloos -Eli Lilly and Company; Eric Stener - Sanofi Pasteur; Fabian De Paoli - CCM28; Jeroen Janssens – GSK; Bernhard Stade - DHL Global Forwarding; Hannes Laessig - Kühne + Nagel; Roland Duquesne - Thermo King
Abstract
Critical design parameters of equipment and operational handling procedures in ocean transportation have a major impact to the airflow and temperature distribution within temperature-controlled ocean containers. ISO 1496-2 compliant and ATO certified 20 foot and 40 foot temperature-controlled containers are the most common for temperature-controlled ocean and sea transport. Each container has a mounted Temperature-Controlled Unit (TCU) at the front to generate enforced temperature-controlled air circulation via the T-bars in the cargo space. Global subject matter experts collected 65 requirements towards container equipment and operational handling to distribute pharmaceutical products at +2°C to +8°C and/or at +15°C to +25°C in these containers. By applying the collected requirements, the pharmaceutical industry and its supply chain partners can harmonize the shipping in temperature-controlled containers and its operational handling. This will improve quality and services, reduce cost and minimize temperature excursions across the supply chain for temperature-controlled containers. Presented requirements may be found applicable to other temperature-controlled container types and sizes as well.
Keywords
Temperature controlled container, 20 ft, 40 ft, requirements, qualification, Temperature-Controlled Unit (TCU), ATO certification, ISO 1496-2 standard, Pre-Trip Inspection (PTI), operational handling, reefer, ocean.
Introduction
Within the pharmaceutical industry, each company has defined its own set of requirements for temperature-controlled containers to transport their temperature sensitive pharmaceutical products at +2°C to +8 °C and/or +15°C to +25°C. These requirements are the result of best practices and executed qualification studies with fully loaded, partially loaded and/or empty containers under summer and/or winter conditions (e.g., hot and/or cold temperature profiles). Various pharmaceutical products had been used during these qualifications, like vials, cartridges, drums and blistered products. With the publication of the revised EU GDP guidance in 20131 and EU GMP Annex 15 in 2015,2 pharmaceutical companies and wholesalers were required to execute qualification studies and to deliver a set of data for temperature-controlled equipment. As each company followed its own approach, different studies were set that resulted in different requirements. As a result, Logistic Service Providers (LSPs) like forwarders, carriers and vessel companies have had difficult times to align all customer requirements for transportation, which can impact services, product quality, safety, and efficacy.
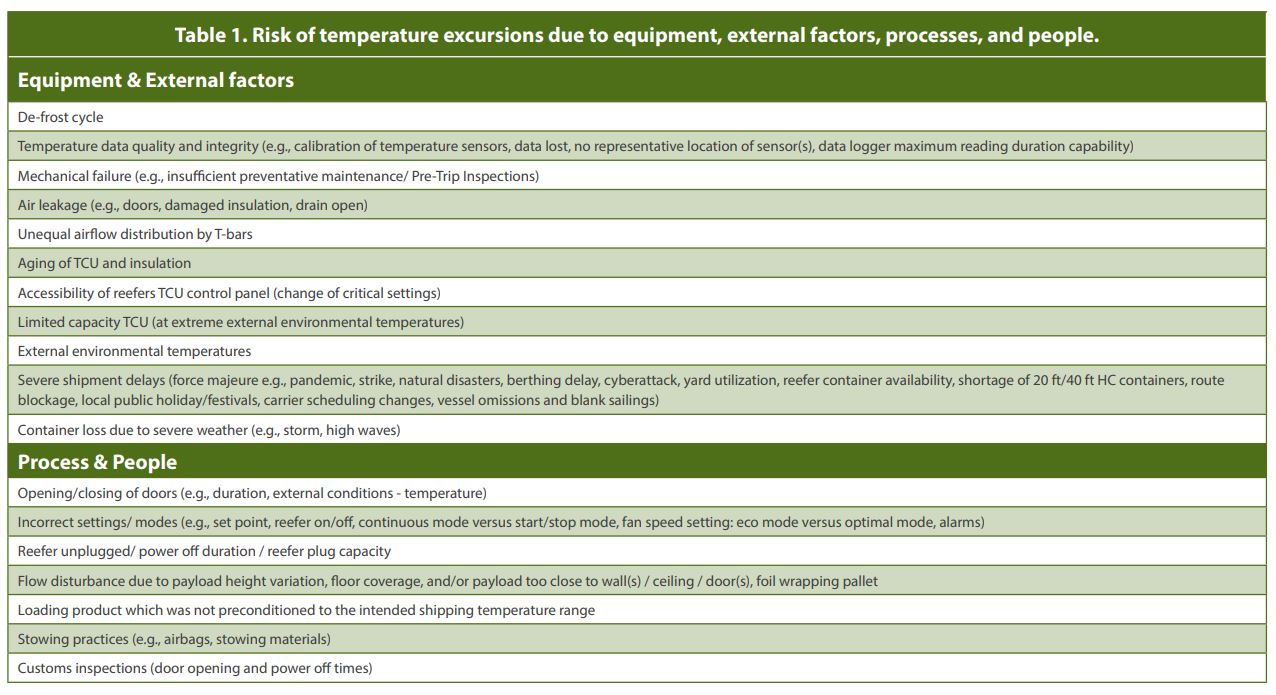
Security risk in temperature-controlled ocean transportation should be considered as well when new transport lanes are developed including loss and missing containers, theft, port and canal congestions, seals, pirate activities and loss of data communication.
Product impact evaluation should be considered in the risk identification while deciding on ocean container usage. Only products with approved risk assessment9 and supporting stability data,10,11 should be considered as suitable for ocean transportation mode.
Selection of Temperature-Controlled Containers
Temperature-controlled containers have insulated ceiling, floor, walls and doors with standard external and internal dimensions according to standard ISO 1496-2.3 These containers have a mounted TCU at the front. In the PDA Technical Report 64,6 six critical design parameters are defined that have an impact on the temperature distribution inside the payload area. These parameters include heat exchange energy, airflow, insulation, thermal integrity, temperature monitoring system and alarms. In Table 2 the pharma requirements for containers and their rationale are listed using the critical design parameters as starting point.
Discussion
Full understanding of supply chain, container equipment, product, and operational handling is essential to control temperatures during shipments and to assess risks. Especially payload stowing, floor coverage, power supply to containers, and container aging can have impact on the temperature distribution inside a container. Therefore, these topics and continuous process verification are subject of more detailed discussion in the sections below.
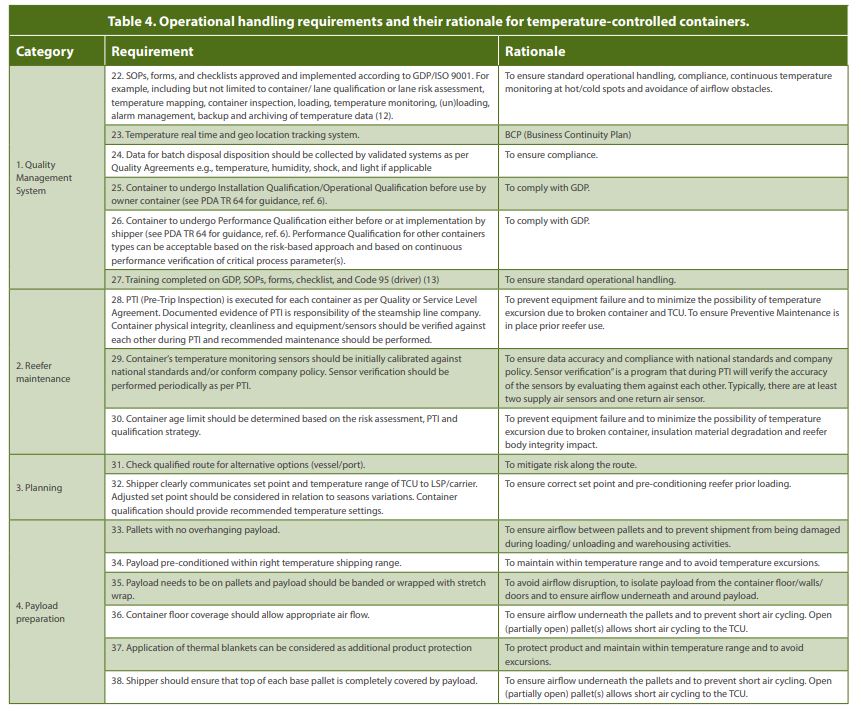
Payload Stowing and Floor Coverage
Appropriate stowing of payload is important in order to secure the position of the payload and to ensure optimal airflow inside the container. During loading and unloading of vessels, containers may experience shocks, drops and unplanned movements due to weather conditions and operational handling. Moreover, heavy stormy weather at sea may initiate movement of the payload that may cause product damage and disturbance of the temperature distribution inside the container. Therefore, stowing of payload should be carefully designed and tested (e.g., airbags usage, supporting materials, strapping etc.). The stowing practice should prevent direct contact between payload and container walls and ensure continued airflow along the payload.
For containers with a floor coverage of less than 95%, an additional floor cover may be considered to enhance airflow distribution through T-bar reefer floor to improve temperature uniformity across payload. Dedicated air flow enhancers as floor covers and dunnage materials close off the right areas of the T-bar top openings and help to guide air across entire reefer floor to the door end. This recommended practice can improve temperature management and mitigate the risk of temperature excursions. Impact of floor coverage has been studied and is described in references 13 and 14.
Power Supply to Containers
In order to maintain the temperature inside a container within the pre-defined temperature range, the container requires power supply from a genset (generator to provide power during transport or when shore power is not available) or electric power from the vessel or at the port. As a container typically changes during a shipment from transport modes, e.g., moving from road by truck to ocean by vessel/ steamship and vice versa, a temperature-controlled container will experience at least four power off events at ports to unplugging and plugging of the container to power supply:
- At the origin port: Container transfer from truck to quay and from quay to vessel
- At the destination port: Container transfer from vessel to quay and from quay to truck
Sometimes containers may be transferred between vessels in a transit port (terminal to terminal), which would add two other power off occasions and additional risk of temperature excursions (see Figure 2). Therefore, it is recommended to use one vessel per shipment and to minimize transshipments.
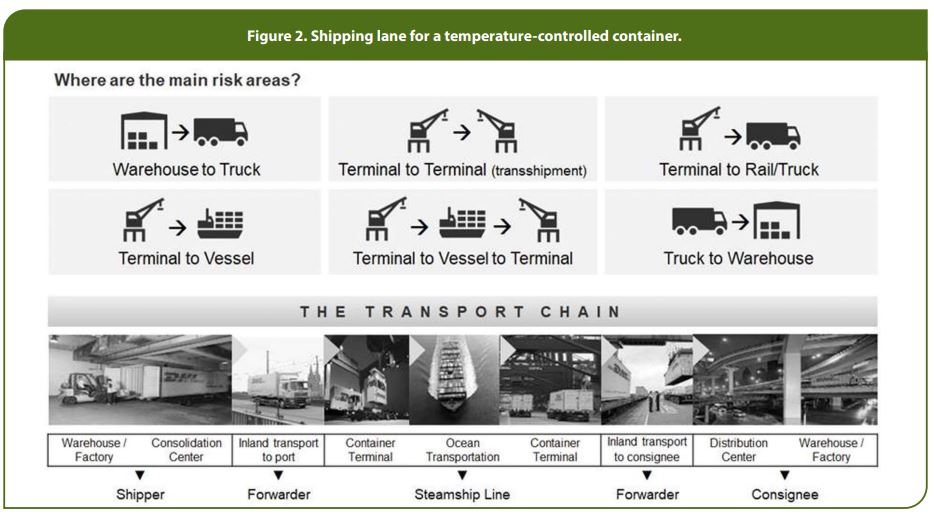
Power off times or the time during which the temperature-controlled container is not connected to an electrical power source may typically vary from one to 24 hours (aggregated) depending on standard port operational procedure duration and container handling cut-off times. The targeted power off times should be between two and four hours per operation in order to minimize risk of temperature excursions and to ensure temperature integrity of the payload. However, the power off time should be considered under a risk-based approach during the temperature mapping study where simulation of power off times shows total recovery time to predefined set point for the container. The total recovery time measured should include all the temperature values recorded from the defined temperature range, i.e., from +2°C to +8°C or from +15°C to +25°C depending on the external temperature conditions. When the total recovery time exceeds the allowable limits, a mitigation plan should be put in place in order to reduce the risk to product quality. Mitigation actions might be the use of additional thermal protection (e.g., thermal covers, thermal packout) or increasing the thermal mass resulting in temperature stabilization.
Container Aging
Many companies in the Life Science and Healthcare industry use or used a container age limit of a maximum of 5 years to mitigate the risk of temperature excursions. This practice may be driven from ATP standard for road trailers, that requires heat-leakage and performance testing after 5 years (initial ATP certificate is valid for 6 years).5,18 The manual twist-locks could be another driver for this limit as they are connected containers on vessels and are often dropped to the next container layer below which can cause dents or eventually holes in the container roof. As a result, the small cracks/ holes enabled water to enter the insulation foam reducing the insulation capacity of the container.
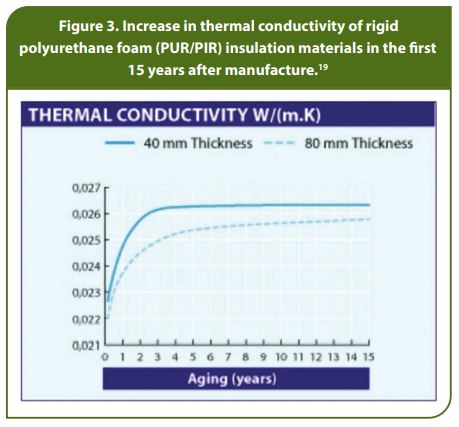
The challenge and discussion point for the industry is how this container age limit could be applied. In today’s shipping industry almost all vessels use “automatic” twist locks which remain on the container and the risk of cracks/holes on the container roof has decreased substantially in the last decade. In addition, reefer containers are built to ISO 1496-2 standard,3 which is generally a higher standard than ATP.5
For each shipment they undergo a steamship-line specific PTI where functionality and equipment is checked on various parameters. Every carrier has a different/individual PTI protocol, but most common procedures for checking are mentioned below and would be repaired/corrected if critical:
- Equipment: fasteners, bolts, hatches, doors incl. rubber-sealing, wiring, outside dents/holes, inside dents/holes, drain-holes, dirt and odor, remaining labels from previous trip.
- Technical: compressor, condenser, TCU, sensors functionality incl. hose, cables, probes, regular service check-up and if any irregularities from previous trip.
The fading of the insulation capability happens over time (see Figure 3). In the first years, the decrease in insulation capability will be strongest, while in the following years it will be less, remaining on a similar level for up to eight years. Insulation deterioration values given in the annex 1 of ISO 1496-2 are the following:
- 2% after 6 months from manufacturing
- 4% after 12 months from manufacturing
- 9% after 10 years from manufacturing.
Container TCUs are built to deliver “over-capacity” to >120% to work against this fading insulation capacity and this is only valid for fully functional and undamaged containers.
The container age is not the only factor at risk of temperature deviations. Other factors may have a more important role in temperature deviations such as payload stowing, floor coverage, thermal mass, external temperatures, and (un)loading practices. It is not practical to determine the number of container trips made before usage, thus if the container was used mainly on long-distance trips or was used more on short-sea connections. As each company has different products, practices and requirements, a risk assessment is recommended to define appropriate container age.
Continuous Process Verification
Continuous Process Verification (CPV) is the collection and analysis of end-to-end supply chain components and process data to ensure
product and transportation outputs are within predetermined quality limits. Its central purpose is to ensure that processes are in a constant
state of control.
As ocean freight transport is highly dynamic with some Critical Control Points of the process uncontrollable (see Table 1), temperature excursions related to operation of the equipment, external factors, processes, and handling staff can be expected. Therefore, the CPV is recommended as a complementary approach to the lane risk assessment and/or transport mode qualification. The CPV on temperature ensures that the container will durably protect the product throughout the shipment from container loading to unloading as intended during the qualification. Temperature monitoring should demonstrate that the state of control is being maintained and equipment is delivering to its intended use. Root cause analysis of temperature excursions will provide knowledge about the risk in shipping lanes, which should be used to update lane risk assessments and take mitigation actions when necessary. For example, temperature excursions may be related to:
- Expected events identified in the lane risk assessment (e.g., power off less than 4 hours, external hot/cold weather conditions).
- Unexpected events not identified in the lane risk assessment (e.g., mechanical failure of TCU, unexpected unplug times).
Based on the root cause analysis and the frequency of temperature excursions, additional mitigation actions may be determined in order to minimize temperature excursions and to maintain product quality.
Conclusion
The TCU operational and usage characteristics as defined by standards and industry recommendations, are part of pharmaceutical industry user requirement specifications. Use of temperature-controlled ocean containers is thus a defined process designed to ensure temperature and safety integrity of the product. Any airflow disruption and deviation from the pre-defined temperature range (set point) can increase the risk of temperature excursions during transport in temperature-controlled containers. Therefore, all efforts should be taken into consideration to ensure the usage of proper equipment, pre-trip inspection, container pre-conditioning and execution of operational handling procedures based on the established requirements. By applying proposed requirements and guidance with transport service providers, the pharmaceutical industry and its supply chain partners can more effectively utilize ocean transport as an alternative to air freight. This will improve services, reduce cost and minimize temperature excursions across the supply chain. Presented requirements may be found applicable to other temperature-controlled container types and sizes.
Acronyms
Acronym - Definition
ATO - Agro-Technologisch Onderzoekinstituut certification
ATP - Assistive Technology Professional certification
CPV - Continuous Process Verification
GDP - Good Distribution Practice
ISO - International Organization for Standardization
PDA - Parental Drug Association
PTI - Pre-Trip Inspection
QMS - Quality Management System
SOP - Standard Operating Procedure
TCU - Temperature Controlled Unit, so called reefer unit
TR - Technical Report
References
- European Commission: Guidelines on Good Distribution Practice of medicinal products for human use, 2013/C 343/01, November 2013.
- European Commission, Directorate – General for Health and Food Safety: EudraLex Volume 4, EU Guidelines for, Good Manufacturing Practice for Medicinal Products for Human and Veterinary Use, Annex 15: Qualification and Validation, March 2015.
- ISO 1496-2:2018 – Series 1 freight containers — Specification and testing — Part 2: Thermal containers.
- Explanatory notes to the ATO certification of reefer containers (version 4.0). See ATO certification at www.reefertransport.nl
- UNECE - Agreement on the International Carriage of Perishable Foodstuffs and on the Special Equipment to be Used for such Carriage (ATP), 2016.
- Parenteral Drug Association Technical Report No. 64 (TR 64): Active Temperature-Controlled Systems: Qualification Guidance, 2013.
- USP 39–NF 34. <1079> Good Storage and Distribution Practices for Drug Products, Rockville, MD: United States Pharmacopeial Convention; 2016.
- HPRA IA-G0011-1: Guide to Control and Monitoring of Storage and Transportation Temperature Conditions for Medicinal Products and Active Substances, 2011.
- Parenteral Drug Association Technical Report No. 58 (TR 58): Risk Management for Temperature Controlled Distribution, 2012.
- Parenteral Drug Association Technical Report No. 53 (TR 53): Guidance for Industry: Stability Testing to Support Distribution of New Products, 2011.
- Van Asselt, E.J. & Bishara, R.H. (2015). Establishing and Managing the Drug Product Stability Budget, Journal of Pharmaceutical Outsourcing, Volume 16, Issue 4, July/August, 2015, 20-27.
- Electronic Code of Federal Regulations (e-CFR): Title 21: Food and Drugs PART 11 - ELECTRONIC RECORDS; ELECTRONIC SIGNATURES
- DIRECTIVE 2003/59/EC OF THE EUROPEAN PARLIAMENT AND OF THE COUNCIL of 15 July 2003 on the initial qualification and periodic training of drivers of certain road vehicles for the carriage of goods or passengers, amending Council Regulation (EEC) No 3820/85 and Council Directive 91/439/EEC and repealing Council Directive 76/914/EEC
- EN 12830: Temperature recorders for the transport, storage and distribution of chilled, frozen, deep-frozen/quick-frozen food and ice cream - Tests, performance, suitability
- Lukasse L.J.S.; Staal M.G. (2018). Optimizing air flow distribution in maritime refrigerated containers. Acta Hortic. 1194. ISHS 2018. DOI 10.17660/ActaHortic.2018.1194.195. Proc. VIII International Postharvest Symposium: Enhancing Supply Chain and Consumer Benefits – Ethical and Technological Issues. Eds.: F. Artés-Hernández et al.
- Lukasse L.J.S.; Staal M.G.; Wissink E.B. (2019). An airflow enhancing floor cover to improve temperature uniformity in maritime refrigerated containers. Proc. of 25th int.’l conf. of refrigeration, Montreal, Canada, paper ID 54. DOI: 10.18462/iir.icr.2019.0054
- ISO 17712:2013(en) Freight containers — Mechanical seals
- Van Asselt, E.J. et al. (2017). Pharma requirements for temperature-controlled trailers, Journal Pharmaceutical Outsourcing, Volume 18, Issue 4, Jul/Aug, 2017, 12-19
- Thermal insulation materials made of rigid polyurethane foam. Federation of European Rigid Polyurethane foam association. Report N°1 (Octobre 06)
Acknowledgment
The author appreciates the permission of using Figure 1 from Kuehne
+ Nagel and Figure 2 from DHL.
Disclaimer
The content and the view expressed in this document are the result of a consensus achieved by the authors and are not necessarily views of the organizations they present or represented.
The mention of a product or service provider does not mean it is the sole product or service that is available for use.