Sachin Misra - Principal & Global Lead - Pharmaceutical, Biotech, and CDMO Industries, Kalypso
The rapid development, manufacture and distribution of vaccines that began in early 2020 to combat COVID-19 showed that perseverance and sheer human will can overcome legacy challenges to meet a global emergency, quickly and safely. While that was something of a landmark achievement, that condensed, pressurized development and tech transfer timeline is neither sustainable nor practical for commercial product drug development and commercialization.
Pressure to go-to-market faster within the pharma industry is nothing new. Even before the COVID-19 pandemic broke, pharma and life sciences companies were working in an ever evolving and increasingly complex environment in terms of regulatory frameworks, supply chain risk and reliability fluctuations, manufacturing complexity, and expansion of network nodes. Factors such as the increase in rare diseases which, according to Rarediseases.org now affect around 1 in 10 Americans, driving a spike in demand for personalized medicines including Advanced Therapy Medicinal Product cell and gene therapies, as well as the emergence of patient-centric value-based healthcare models focused on the quality of care and outcomes, add additional strains to the pharma industry.
Pharma 4.0 and Digital Knowledge Management
To meet increasingly demanding conditions, pharma manufacturers have started to embrace the principles of modernization, autonomy and digitization – which incorporates connectivity, advanced analytics, automation, and advanced autonomous manufacturing.
They are integrating elements such as industrial internet of things (IIoT) across the manufacturing floor and into daily production and distribution routines to drive transformation efforts and deliver new levels of agility. In 2017, the International Society for Pharmaceutical Engineering (ISPE.org) provided quality-centric guidance promoted in ICH guidelines Q10, Q11, and Q12, use cases, alongside a roadmap for the pharma industry to embrace digital management of their operations, creating the perfect context for Pharma 4.0.
The adoption of Pharma 4.0 envisions pharmaceutical manufacturing facilities that offer the power of seamless connectivity across the value chain, leveraging digitized product and process data and enhanced processes to deliver actionable analytics as an essential part of the connected enterprise. This helps optimize quality management, data integrity and productivity to support more flexible and efficient operations capable of handling today’s rigorous and fast-changing production needs.
Digital Knowledge Management provides clarity in a single source of truth for digitized product, process, and packaging definitions, allowing enterprises to efficiently implement change control and collaboration across the value chain. It organizes, standardizes, and streamlines the information required to define a product and the processes to manufacture it. This typically includes, for example, the product’s physical and chemical specifications, critical quality attributes, critical process parameters and setpoints, manufacturing requirements, standard operating procedures (SOPs) and the management of variability in those data sets from line to line and plant to plant while supporting multiple regulatory requirements.
Historically, transitions or tech transfers between development and manufacturing stages were mostly managed in silos, as they were manually packaged and repackaged in order to suit the needs of the next stakeholder in the value chain. The disconnect between business functions, technology solutions, and processes often resulted in errors throughout the discovery, design and manufacture of pharmaceutical products, ultimately resulting in loss of data integrity. All of which lead to greater costs, longer cycle times, increased manual efforts to ensure multi-site manufacturing, and lack of incentive for product and process improvement.
Laying down a digital foundation for innovation that combines the benefits and intelligence of Digital Knowledge Management and Pharma 4.0, companies can achieve comparable results to those seen through the delivery of COVID-19 vaccines, and provide them in a sustainable, efficient and profitable way.
How is This Possible?
The protocols, advanced technologies, digitization and connectivity, in tandem with the defining clarity of Digital Knowledge Management, now position pharma manufacturers to address these core industry challenges more holistically and efficiently than ever before.
Using Digital Knowledge Management to create and enable a digital product definition along with all its processes, R&D and manufacturing can ease the burden of enterprise change control and increase collaboration across the value chain. This offers important benefits such as reduced process design cycle time, integrated quality controls, simpler and faster technology transfer, more efficient manufacturing and continued progress to enterprise data integrity.
Building on the aforementioned digital foundation, pharma manufacturers can generate a ‘digital thread,’ a seamless flow of data that connects business processes across the entire value chain. This thread spans the entire value chain of discovery, development, manufacturing, and sales. It encompasses key processes including recipe and process development, tech transfer, plant and process engineering and scalability. The net result is the establishment of a pervasive ‘digital fabric’ that sits across an enterprise, improving operational resilience and positioning organizations to be able meet both present and future challenges.
Challenges can be remedied by weaving the digital thread, built on the foundation of Digital Knowledge Management, across the multiple systems used throughout a product’s lifecycle into cogent digital data streams. This process transforms data from a required output into a valuable asset from which the digital thread can glean invaluable and competitive insight. These systems can include:
- Recipe authoring tools
- Process Knowledge Management tools (PKM)
- Laboratory Information Management System (LIMS)
- Electronic Lab Notebooks (ELN)
- Product Lifecycle Management Systems (PLM)
- Regulatory Information Management (RIMS)
- Clinical Trial Management Systems (CTMS)
- Manufacturing Execution Systems (MES)
- Enterprise Resource Management (ERP)
This integration of systems, sometimes referred to as a Digital Knowledge Center, is vital to implement change controls and other tracking mechanisms that authoring tools normally do not offer. With this ecosystem of digital data, the digital thread becomes a rich current of data, and a valuable asset that enables manufacturers to derive greater value from adjacent technologies while ensuring data integrity.
Summarizing the Process
Realizing the benefits of Digital Knowledge Management is a logical process, summarized as follows:
- The first element required is the foundation of a single, digitized, and structured source of truth for pharmaceutical product, process, and packaging definitions. This is critical to generate a continuous digital thread.
- The resulting digital thread architecture will have Digital Knowledge Management tenets at its core and define the roadmap for the digital transformation journey.
- Next, building a business case is normally required to review and align priorities with executives, secure their buy in and begin to mobilize a team to activate the digital thread.
- Developing a structured Digital Knowledge Management data model enabling the management and change control governance of market specific materials, processes and localized equipment per ISA standards (88, 95, 99) is next. It sits at the core of a typical digital thread journey.
- With this foundational capability in place, it is possible to begin sequentially connecting the digital threads, allowing for collaboration with manufacturing plants and CDMOs, integration with other enterprise tools such as ERP, LIMS, MES, and RIMS, and the establishment of more advanced capabilities such as artificial intelligence for process and materials optimization.
- Through establishing product and process data, change management, data governance and data exchange mechanisms across the digital value chain, the continuous digital thread will eventually eliminate the need for singular tech transfer events and enable the secure publication and consumption of digital data on demand.
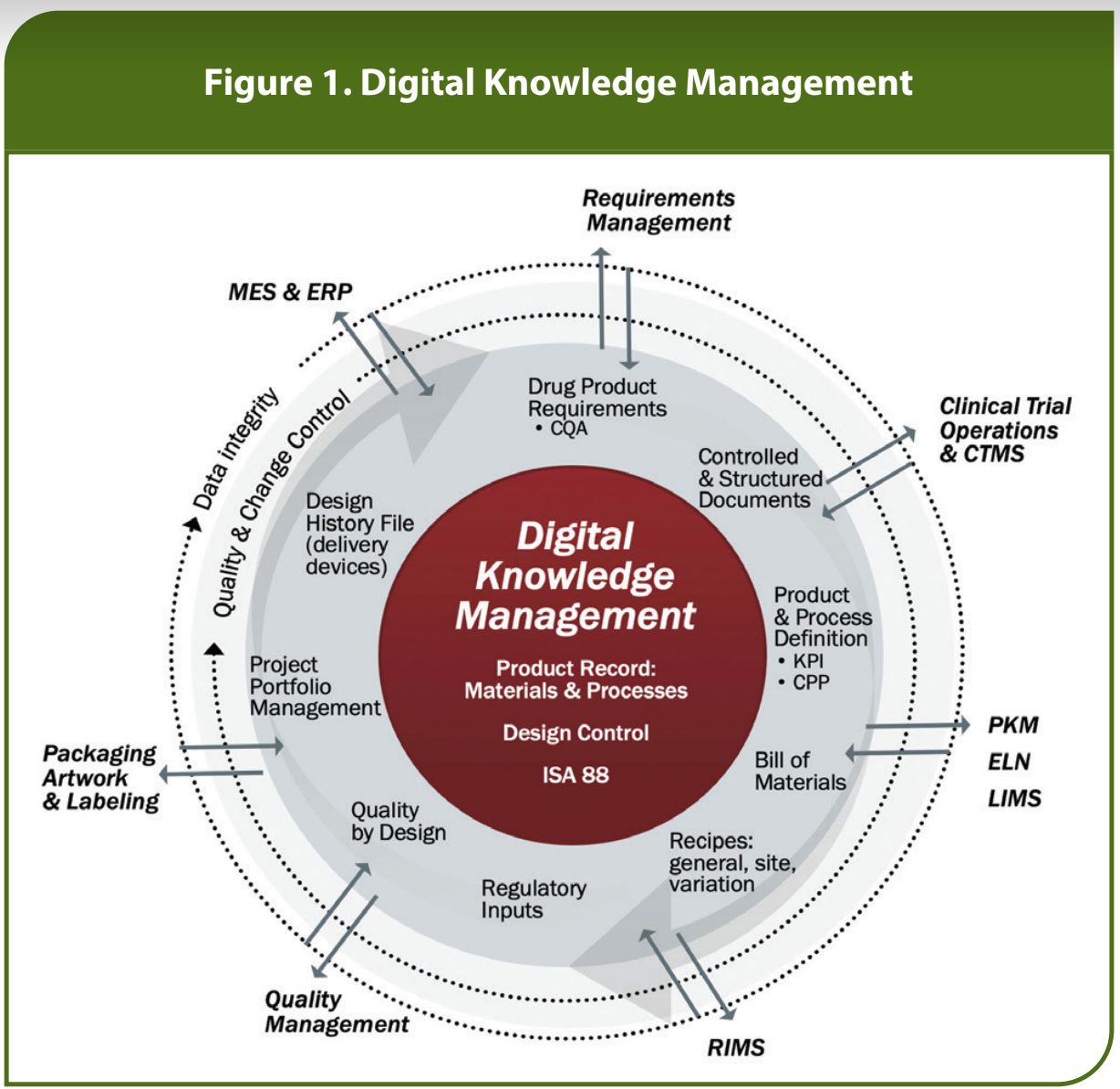
Value Chain Benefits
Enabling and strengthening Digital Knowledge Management offers benefits along the entire value chain. By removing operational and communication silos, empowering cross-functional collaboration through a reliable single source of truth results in lower costs and the mitigation of risks to quality and product safety.
One practical example of the benefits of Digital Knowledge Management is the digitization of work instructions. In a traditional work environment, employees on the manufacturing floor may have been issued work instructions that could have undergone lengthy change control exercises. These work instructions are typically printed or delivered as a “paper on glass” electronic document. If communications relating to working instructions are inefficient or not fully connected, operators may be working with outdated and out-of-compliance information. So, if regulations change or there’s a new way to lower the cost of a recipe, the cost and time of siloed changes and the eventual reprint of thousands of copies and manual retraining can be significant, not to mention that products might not be compliant as they don’t meet the most current specifications.
Digital Knowledge Management not only eliminates the need for paper-based work instructions, but enables early prediction of recommended recipe changes, prompts and tracks approval of those changes, and relays those changes immediately to all relevant stakeholders across the enterprise, regardless of location. This saves time throughout the change control process, eliminates time wasted trying to track down the latest source of truth, enables management and executive visibility into the status and priorities of emerging projects and changes, and expedites the communication between R&D and manufacturing.
Finally, and most importantly, Digital Knowledge Management serves as the launch point for a digitized technology transfer process by:
- Managing product, process and packaging design knowledge in a single source of truth repository;
- Undergoing a harmonized cross-functional change control process;
- Collaborating and centralizing cross-functional materials, process, and packaging knowledge and ensuring that manufacturing can rapidly scale across global manufacturing sites and lines.
As a result, tech transfer lead times are reduced, reliability is improved and product risk decreases.
The bottom line for pharma manufacturers here is that embracing the digital thread and establishing a digital fabric across the enterprise is now necessary to meet the challenges of the present and future. Some pharma firms have already started to realize the benefits of the digital thread, and those who have a solid data foundation of digital knowledge management will be more prepared and more resilient – whatever happens in the future.
Sachin Misra leads the global pharmaceuticals and biotech industry practice and co-leads the life sciences practice at Kalypso: A Rockwell Automation Business. He brings over 25 years of experience in digital value chain advisory services and technology implementations.
Subscribe to our e-Newsletters
Stay up to date with the latest news, articles, and events. Plus, get special
offers from Pharmaceutical Outsourcing – all delivered right to your inbox! Sign up now!