The biopharma industry’s continuing focus on productivity and efficiency is driving manufacturers to focus on core competencies and to consider outsourcing activities that can be handled more effectively by contract manufacturing organizations (CMOs). As a result, outsourcing has become an increasingly common strategy for biomanufacturers.
In our 14th Annual Report and Survey of Biopharmaceutical Manufacturing Capacity and Production,1 outsourcing trends have been analyzed since 2006, and data show that biomanufacturers have been generally outsourcing more each year. In 2006, for example, 57.6% of biomanufacturers did all their mammalian bioprocessing in-house. Eleven years later, after a continuing decline, in 2017, we find that only 44.2% do 100% of their manufacturing themselves (See Figure 1).
Figure 1. Biopharmaceutical Manufacturing Facilities Outsourcing NO Production, 2006-2017Traditionally, biopharmaceutical companies outsourced tasks that were repetitive, that could be handled easier or cheaper elsewhere, and that were not within their core competencies. Today, biopharmaceutical companies outsource all manner of activities, including process development, assay and testing services, R&D, validation, bioprocessing design, and fill-finish, among others. Manufacturers can use outsourcing to eliminate the need of building costly specialized facilities or hiring and training staff. Outsourcing then frees up staff, facilities, and resources to focus on the key elements of the company.
Our Annual Report shows shifts in outsourcing trends as CMOs adopt new technologies, and acquire highly sophisticated skills that not only increase capacity and increase efficiency, but also expand a manufacturer’s offering. Biopharmaceutical manufacturers are reporting their use of outsourcing as a manufacturing strategy rather than simply a method of adding flexible capacity or reducing overhead costs.
This analysis provides insight into the future of the industry as a whole. And while the general trend appears to be an increase in outsourcing, the details provide a clearer picture of this complicated issue.
Although over the past 11 years, microbial fermentation, plant, insect and yeast platforms have all generally shown decreases in the number of companies doing 100% of their manufacturing in-house, we did see microbial fermentation increase this year in terms of the percent doing all manufacturing in-house.
In addition to assessing how much biomanufacturers are outsourcing, we also wanted to know what specific activities are being outsourced. In looking at 24 different categories of outsourcing activities, several are outsourced by nearly all biomanufacturers to some degree. The top activity was analytical testing, of which 90.4% of survey respondents said they outsourced at least part of that activity.
Other highly outsourced activities included toxicity testing (80.9%), and fill/finish operations (73.4%). These results show that the dominant outsourcing activities tend to be restricted services where a high degree of specialization may be required, such as fill/finish. Conversely, the three activities listed as having the lowest percentage of outsourcing by biomanufacturers were downstream process development (31.9%), design of experiments (33.0%) and upstream process development (36.2%). The analysis here suggests that these complex functions largely stay in-house at the company, at least for now.
Figure 2. Selected Data-Percent of Biomanufacturers Outsourcing at Least Some Activity Today
Figure 3. Selected Data: Average % of Activity Outsourced TodayThese activities over the past seven years have been relatively consistent, with analytical testing always reported as one of the top activities outsourced almost every year. Similarly, toxicity testing and fill/finish operations have also been at the top of the list. Downstream and upstream process development and design of experiments have also nearly always been toward the bottom in terms of number of companies that outsourced those activities. BioPlan also asked biomanufacturers how much of a specific activity is outsourced. The top response was fill/finish operations, in which the average percentage of fill/finish operations that were outsourced was 30.5%. Keep in mind that operations such as fill/finish are often either all-outsourced, or mostly inhouse so the average numbers may reflect a bimodal distribution. Toxicity testing and analytical testing were also at the top, with an average percentage of 29.4% and 29.1%, respectively. This means that approximately just under a third of these activities are being outsourced, and that a full two-thirds of these activities remain in-house.
Interestingly, while the overall trend has been toward an increase in outsourcing in general, the general trend of the percentage of each activity that is outsourced has not changed much since 2010, and in many cases, it has decreased. This could mean that while companies are turning more and more toward outsourcing, they are still only using it for the lower value, lower risk parts of each of their activities rather than outsourcing entire processes and departments.
Problems with Outsourcing
Outsourcing can be a signal of a strong biomanufacturing industry. It can indicate that companies have enough demand for quantity or variety of product that they turn to CMOs to take care of activities they no longer see as a core operation, or that others are more competent to perform. Some believe too much outsourcing may weaken facilities and leave companies with too few real assets. Outsourcing, clearly, leads to having fewer in-house capabilities. This results in companies having to bring in CMOs or consultants to fix problems that would traditionally be handled by in-house staff. Some companies seek to retain in-house knowledge and skill while also not having to eliminate the flexibility that comes from having some in-house infrastructure and staffing for manufacturing.
Outsourcing can address problems of capacity limitations, decrease overhead costs, and permit production when in-house capabilities are limited or simply lacking (such as with smaller organizations). But it also has its own set of problems. Asking what the critical issues were in selecting a CMO for outsourcing, 71.6% of manufacturers noted that protecting intellectual property was “very important.” Others were concerned for operational issues, such as effectively handling crosscontamination issues and complying with quality standards.
Protecting intellectual property has been a top issue since 2009. Manufacturers are clearly concerned that their products and processes remain proprietary and are not adopted by the CMO or shared with other clients. Cross contamination is obviously an industry-wide issue that surely occurs at the manufacturers facilities themselves. It may be that there is a lower overt tolerance for it when outsourcing the activity versus dealing with the issue in-house.
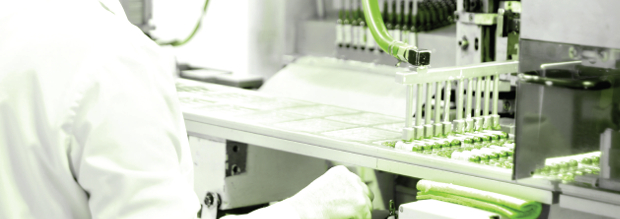
Future Trends in Outsourcing
It may be difficult to predict the future trends in outsourcing given the changing regulatory landscape, the emerging overseas markets, and factors like biosimilars just beginning to emerge. However, based on current knowledge, manufacturers were asked to consider which manufacturing activities would be outsourced within the next five years (by the year 2022). A majority of companies (70.9%) said they anticipated at least part of their mammalian cell culture operations would be outsourced. This is very consistent with past years, and has shown a general increase since 2012. So the Mab outsourcing trends are expected to continue.
On the other hand, microbial fermentation was predicted to have a significantly lower amount of outsourcing compared to the last few years (38.9% vs. 78.1% last year). It will be interesting to see if this actually occurs and whether the prediction remains the same over the next few years.
Another future trend that may take center stage is offshoring of bioprocess operations. In our study, we found that biomanufacturers in the US identified their top five locations for international expansion in the next five years to be:
- Ireland
- China
- Singapore
- Japan and
- UK
Interestingly, manufacturers in Western Europe listed as their top 5 locations of international expansion:
- US
- China
- Germany
- Singapore, and
- Ireland
This trend will be interesting to watch as capacity in emerging markets, such as China and India, begin to achieve Western and GMP standards. These developing regions are improving their biomanufacturing competence first to fulfill their own domestic market needs, through the production of biogenerics. According to our recent analysis of China biomanufacturing2 the great majority of Asian manufacturers within the next five years plan to target production and exports of biologics to Western Europe and the US, these will likely involve the marketing of biosimilars that are developed and manufactured to GMP standards.
Conclusions
Outsourcing for production of biologics clearly will continue, and become more important as more and smaller companies look for opportunities to enter the market and get their products into clinical trials. Larger companies will look to outsourcing to manufacture their established products so they can free up capacity in their own facilities for new products. New manufacturing platforms could potentially impact the current CMO industry as novel expression systems become viable alternatives to traditional mammalian, yeast, and bacteria systems. For example, a number of vaccines are in development using a variety of plant expression systems. And with plants able to make recombinant proteins at a lower cost, in vast quantities, and with these technologies approaching commercialization, biopharmaceutical developers may begin to more seriously consider their use.
Outsourcing of various operations, whether to local CMOs or offshore, will continue to increase. To address this increasing demand, CMOs have become an integral part of many of their clients’ production strategies, and that trend is likely to continue as biologics become more specialized, with more skill and perhaps smaller amounts being required.
References
- 14th Annual Report and Survey of Biopharmaceutical Manufacturing Capacity and Production, BioPlan Associates, April 2017, 476 pages.
- Top 60 Biopharmaceutical Facilities in China, 2nd edition, BioPlan Associates, February 2017, 375 pages.
Eric S. Langer is president and managing partner at BioPlan Associates, Inc., a biotechnology and life sciences marketing research and publishing firm established in Rockville, MD in 1989. He is editor of numerous studies, including “Biopharmaceutical Technology in China,” “Advances in Large-scale Biopharmaceutical Manufacturing”, and many other industry reports. [email protected] 301-921-5979. www.bioplanassociates.com
Survey Methodology: The 2017 Fourteenth Annual Report and Survey of Biopharmaceutical Manufacturing Capacity and Production yields a composite view and trend analysis from 227 responsible individuals at biopharmaceutical manufacturers and contract manufacturing organizations (CMOs) in 25 countries. The methodology also included over 131 direct suppliers of materials, services and equipment to this industry. This year's study covers such issues as: new product needs, facility budget changes, current capacity, future capacity constraints, expansions, use of disposables, trends and budgets in disposables, trends in downstream purification, quality management and control, hiring issues, and employment. The quantitative trend analysis provides details and comparisons of production by biotherapeutic developers and CMOs. It also evaluates trends over time, and assesses differences in the world's major markets in the U.S. and Europe.